We have a big basement, which is unusual for the Pacific Northwest (i.e., no tornadoes, so why worry). However, when we lived in Denver we got used to having one, so how much could it cost to dig a bit deeper. Well, a lot it turns out. Extra to dig, extra to haul away 260 cubic yards of excess material (and find someone to take, not buy, it) and a bunch extra for 112' of 4' high concrete wall and a 30' x 26' slab. All told, I suspect it was a $10-15k add on. So we better use it, and appropriately. We used about 20% of it for the mechanical elements of the house: hot water boiler, radiant heat distribution, central vacuum, and eventual water conditioners. We partitioned off a 10' x 10' room for a wine (beverage) cellar since the basement is unheated. Heck if those fancy wine guys in Napa can have caves, we'll have a cellar. That left about 1/2 of the basement for storage, but the space is big and tall enough for a entertainment room (pool table) or workshop.
To complicate matters, when we bought our appliances from Fredricks in Redmond they sweetened the deal by throwing in a wine cooler and a microwave. Didn't need the cooler but agreed that the microwave could live in the butlers pantry. Some how it doesn't seem right to see a microwave and a 6-burner Wolf rangetop in the same room. We mainly use one for defrosting, heating up fluids, and leftovers for lunch. Free is free, so how could we lose.
The wine cooler turned out to be a refrigerator size unit capable of storing 144 bottles. Just enough for your average party. It was 6' high, 2' wide and 2' deep. I say was, cus I off loaded it on Craigslist today. Say what your want about Craigslist taking down the regional newspapers, but it's one efficient and cheap (free) way to sell stuff. Over the past 3 years I've sold about 100 items on it (no kidding), including 3 cars, 4 pinball machines, old furniture (a favorite), and all kinds of miscellaneous stuff. Usually there is no or only minor haggling about the price. Also its nice since you don't have to actually meet the buyers until the deal goes down; all the prelims are done anonymously. Cash is king.
So on Thursday evening, in a Trypyophan stupor (chemistry.about.com/od/holidaysseasons/a/tiredturkey.htm), I posted the wine cooler on Craigslist with a couple-paragraph explanation but no picture since the unit is still boxed up. Set the hook and dangled it out there on the ethernet. By the morning I had one bite and three nibbles. The bite was from a women in Seattle that was setting up a home-wine tasting business and needed some way to keep lots of bottles of wine cool. Apparently, but law she has to have $3000 of inventory on hand to be legit. Sounds like a little wine store to me. Anyway, she bought it sight unseen, and arrived at noon with cash in hand. I help her husband load it into the pickup truck, tie it down and watched her drive off. Kachinge. Now I have money to build wine racks and a table in the cellar.
Building a House in Kala Point, Port Townsend, WA
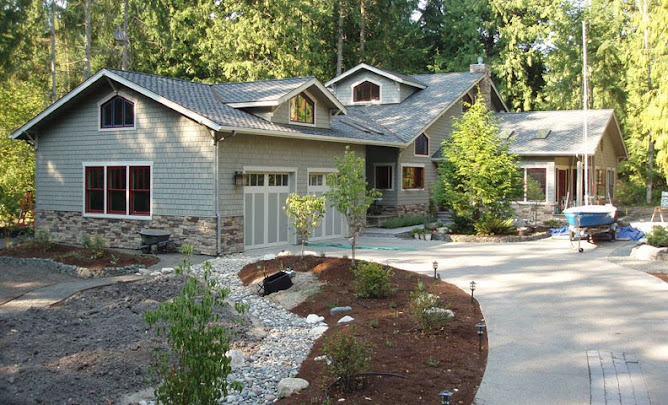
A running narrative of first-time builders of their retirement home in Port Townsend, WA (NE corner of the Olympic Pennisula, 60 miles NW of Seattle). Follow us as this adventure unfolds in late 2008 and beyond. 18 months under construction, we moved in on May 25th, 2010. Photo taken August 15, 2010.
Search This Blog
Saturday, November 28, 2009
Friday, November 27, 2009
Jammin (sung to Bob Marley) Day 397
Before Turkey Day I'd built the window jambs out in the bathroom and really struggled. Built them thicker than needed, then planed them down to be flush with the drywall. Big mistake (no. 1.1). I realized that I should just make them stand 1/16" proud, then back caulk any gap that might form behind the final trim. Duh!
So today I took the new approach to the window jambs. Did 5 in one short day, which was about one an hour. Not bad, but it seemed ironic that as I started the first one an old Bob Marley tune came on the light jazz station— specifically Jammin:
Ooh, yeah! All right!
We're jammin':
I wanna jam it wid you.
We're jammin', jammin',
And I hope you like jammin', too.
Holy Shit! That was definitely a karma moment. Yeap, built 5 jambs, attached them and didn't screw up a single one!. By 3 pm, I figured I had tested my luck, so I bailed out and went to Carls for more jamb lumber (1x5 vg hemlock). All set to do the last 2 downstairs, then tackle the garage and upstairs (10 more windows).
On another positive note, I off loaded the 144 bottle wine cooler that Fredricks Appliances had thrown in on our appliance package. Since we have a space dedicated to a wine cellar in the basement, why would you want to use voltage to keep wine cool. I posted the sucker (new in box) on Craigslist at 5 pm last night, and had 4 offers to buy it by this morning. Sold it to the first person for cash and it left the garage at 1 pm. Damn, I love Craigslist even if its going to run all the big newspapers out of business.
So today I took the new approach to the window jambs. Did 5 in one short day, which was about one an hour. Not bad, but it seemed ironic that as I started the first one an old Bob Marley tune came on the light jazz station— specifically Jammin:
Ooh, yeah! All right!
We're jammin':
I wanna jam it wid you.
We're jammin', jammin',
And I hope you like jammin', too.
Holy Shit! That was definitely a karma moment. Yeap, built 5 jambs, attached them and didn't screw up a single one!. By 3 pm, I figured I had tested my luck, so I bailed out and went to Carls for more jamb lumber (1x5 vg hemlock). All set to do the last 2 downstairs, then tackle the garage and upstairs (10 more windows).
On another positive note, I off loaded the 144 bottle wine cooler that Fredricks Appliances had thrown in on our appliance package. Since we have a space dedicated to a wine cellar in the basement, why would you want to use voltage to keep wine cool. I posted the sucker (new in box) on Craigslist at 5 pm last night, and had 4 offers to buy it by this morning. Sold it to the first person for cash and it left the garage at 1 pm. Damn, I love Craigslist even if its going to run all the big newspapers out of business.
Sunday, November 22, 2009
Major screw up (Day 392)



Thursday, November 19, 2009
Red Birch Flooring (Day 389)
On Tuesday (Nov. 17th), Mike Mills of Mills Interiors (Hardwood, Bainbridge Island) showed up to start the hardwood flooring install. Him and another guy jumped on it, and 6 hours later they had laid about 1/3 of the flooring. This involved the hall like run of flooring next to the kitchen tile (photo 1) and parts of the living room and den (photo 2).
Had to have them reinstall the floor header (perpendicular to flooring strips) around the fireplace where the hearth will go. I had laid it out at 12" x 5', and it didn't look right. By the time I returned after lunch, they had this done, but no worries. They ripped it up, pulled out one strip and relaid the hearth frame at 18" x 6 ft. This way we can use full 18" square tiles on the hearth and allow the fireplace mantle to rest on wood or tile. In reality, the mantle and hearth should be in, then they could just put the flooring around them. Mistake diverted, but just barely.
By Thursday afternoon, they had laid all the wood that was delivered, but were still about 75 sq. ft short. This is a sign of the times; wasted wood (or any product) comes off the bottom line (profit) for them. So he ordered enough red birch to finish the job after Thanksgiving. No hurry on our part since we had lots to do before the door frames go in. Before we hang the doors, we'll need to have all the flooring in place; that includes the wood and ceramic tiles. Since we haven't even shopped for tile, we're at least a month out on doors. In the den, we won't have a hearth since it would eat up a fair bit of the room. These gas fireplaces don't require a hearth, so Mike just picture framed around the fireplace to finish off the flooring (second photo).
The floor looks great. Went with a no. 1 (not select) product, which shows more grain and notes than the select grade. Saved a few bucks and it gives the floor more character. The select grade was nice, but a little monotonous when laid out in big sections. They won't do the floor sanding until all the trim work and painting is done. We'll have them apply a satin finish (either polyurethane or an oil-based product) at the end; a first coat after sanding then a final coat just before we move in, which is looking like about Day 940 (May 1, 2010). However, eagle-eye Nancy noticed that there is a $6500 IRS credit for move-up house buyers (owner builders included) if you occupy by April 10, 2010, so there may be a pretty good reason ($$$) to occupy the house by this date. More on this later.

The floor looks great. Went with a no. 1 (not select) product, which shows more grain and notes than the select grade. Saved a few bucks and it gives the floor more character. The select grade was nice, but a little monotonous when laid out in big sections. They won't do the floor sanding until all the trim work and painting is done. We'll have them apply a satin finish (either polyurethane or an oil-based product) at the end; a first coat after sanding then a final coat just before we move in, which is looking like about Day 940 (May 1, 2010). However, eagle-eye Nancy noticed that there is a $6500 IRS credit for move-up house buyers (owner builders included) if you occupy by April 10, 2010, so there may be a pretty good reason ($$$) to occupy the house by this date. More on this later.


Monday, November 16, 2009
Hardi, Har, Har (Day 386)

[P.S. There is un problemo. I thought the kitchen tile was 1/4", but the hardwood guys say floor tile is 3/8", so I should have used 1/4" backer board. Oh well. The flooring guys will make thresholds for the two places where there are transistions (master bath to master bedroom, and guest bath to great room floor. I can return the remaining 1/2" Hardibacker board for 1/4" so there won't be any elevation changes from the kitchen tile. I can live with this.)
Well, after the HD guys loaded the board, the tires were pretty low. Went over to Costco, which is always the second stop on our trips to Sequim. The guys at the Tire Dept. pumped up the tires from 20# to 55#, and noticed that one of the lug nuts was almost off. Looks like I should have been doing some maintenance on the trailer, in advance. They torqued all the nuts, we did a visual on the lights and all was well. The load trailered nicely on the 25 mile trip home. However, when I looked up the specs on the Hardibacker board for installation, I noticed that they weight about 40# each. So the real payload was about 1800 pounds, plus another 80 pounds of paint (2-5 gal buckets). I guess I'm lucky I got it all back to Port Townsend in one piece.
I started the tile backing board project by laying out the sheets, as efficiently as possible on the floors. You don't want any four-way corners as they are weak points, so you need to stagger boards. I cut and laid out all of the board board in a half day, which seemed pretty fast. This even included cutting two sheets with circular holes for the toilets. The fastest way to cut these holes is with a Sawzall and narrow blade. 30 seconds and you're done. As for cutting the board, Hardi Corp suggest using a carbide bladed knife to score the board, then breaking it. That might work well for the 1/4" stuff, but not the 1/2" board. I resorted to my battery powered circular saw with a carbide bit. It throws off a lot of dust, but its only Portland cement and sand so a dust mask is advised.

On Tuesday, the hardwood installers are coming over to lay the job out, and perhaps nail a few in. That's another blog for another day.
Thursday, November 12, 2009
We score a Trifecta (Day 382)
Today we scored a trifecta, of sorts. Actually a quadfecta, if there was such a thing. Nancy and I finished painting the man cave (room above the garage, mainly for building kayaks and other manly things). Still have to paint and trim out the windows, add flooring and baseboard, but all that will have to wait for additional funds. I figure if we recycle all the aluminum cans from our house, we'll have the money for this in about 2060.
As for the trifecta part, it went this way:
1) Picked up the 6 cabinets for the master bath from the Kitchen and Bath Studio in PT. Cherry shaker style cabinets with medium stain and lacquer finish. Two 18' wide (21" deep) drawer units, two 30" wide sink bases (21" deep), a central drawer unit that is 6" taller and deeper (24"), and a linen closet (24" wide, 84" high), all with toe kicks. Since these are a manageable lot, I think we'll install them first as a test for the bigger assemblage of cabinets in the kitchen, pantry, and mudroom. The countertop will be an Italian banded travertine. We picked out the slab from Metagranite in Seattle, and Richerts in Sequim will do the cutting and installation hopefully towards the end of November.
2) They hid the hose. We'd earlier had a central vacuum system installed by A-B Vacuum of Puyallup (still can't pronounce this one). The did all the piping before drywall, then needed to return to install the cover plates, the vacuum unit, and hoses. These are quite cool—the hose retracts into the piping. We saw it at the Seattle and Denver home shows over the past few years, and the system was priced comparably with standard, haul the hose systems. Anyway, they'd had a cancellation on an install that day so they decided to come up. Three hours later, they were installing, testing and teaching us how to use the thing (simple).
3) The hardwood flooring arrived from Seattle. It was supposed to be here in the early afternoon, but they got buggered up with closure of the Hood Canal bridge for 90 minutes (testing). It was dark by the time they arrived, but we unloaded 1000 sq. ft (3000 linear ft) of red birch flooring. It is standard nail-down stock; 4" wide, 3/4" thick, tongue and groove. We stacked it up in three piles on the radiant flooring to dry out in the next week, prior to installation by Mills Interiors, Bainbridge Island (flooring and tile). We'll have the floor installed now, then sanded after all the door jambs and tile is installed. That should be months away at my pace of work. Hopefully, the installers will be more carefully than Classic Hardwoods of Sequim. They did the Christophers house in PT in June and managed to hit Pex tubing in four spots. I'll be watching carefully, like an old grandmother.
Now that the garage is back in a usable condition, we'll start to move the kitchen cabinets (39 boxes) over from the rental property. All the appliances are already on site, so the garage is going to be filled up soon. I set up the chop saw and table saw in the pantry, which will become the new workshop for all the remaining trim work.
As for the trifecta part, it went this way:
1) Picked up the 6 cabinets for the master bath from the Kitchen and Bath Studio in PT. Cherry shaker style cabinets with medium stain and lacquer finish. Two 18' wide (21" deep) drawer units, two 30" wide sink bases (21" deep), a central drawer unit that is 6" taller and deeper (24"), and a linen closet (24" wide, 84" high), all with toe kicks. Since these are a manageable lot, I think we'll install them first as a test for the bigger assemblage of cabinets in the kitchen, pantry, and mudroom. The countertop will be an Italian banded travertine. We picked out the slab from Metagranite in Seattle, and Richerts in Sequim will do the cutting and installation hopefully towards the end of November.
2) They hid the hose. We'd earlier had a central vacuum system installed by A-B Vacuum of Puyallup (still can't pronounce this one). The did all the piping before drywall, then needed to return to install the cover plates, the vacuum unit, and hoses. These are quite cool—the hose retracts into the piping. We saw it at the Seattle and Denver home shows over the past few years, and the system was priced comparably with standard, haul the hose systems. Anyway, they'd had a cancellation on an install that day so they decided to come up. Three hours later, they were installing, testing and teaching us how to use the thing (simple).

Now that the garage is back in a usable condition, we'll start to move the kitchen cabinets (39 boxes) over from the rental property. All the appliances are already on site, so the garage is going to be filled up soon. I set up the chop saw and table saw in the pantry, which will become the new workshop for all the remaining trim work.
Thursday, November 5, 2009
Cleaning house (Day 375)
Only time for a quicky post.
In order to save a few bucks (i.e., beer money) I told our painter that we'd clean up after he finished. No big deal, just some paper on the floors and plastic on the windows. Oh yeah. Nancy and I spent most of today (Thursday) pulling down plastic, pulling staples and ripping up paper. Interestingly, the thin Kraft paper that Franks daughter laid down to protect the floor did a pretty good job where it stayed down or in place. After a few coats of paint dried on it, the paper was more like a thin tarp. This made it easy to just fold it up into reasonable size bundles and load up the trailer for another dump run. We put the 14 empty paint pails (5 gals) in the trailer, but I discovered that its rated as recyclable so I'll try to unload that stuff for free. Now the shop vac is coming out for a final cleanup before the flooring gets delivered next week. By the way, that shop vac is the 5 HP, 10 gal one I bought from Sears to remodel the Denver house in 1976. 33 years old, butt ugly, but it still sucks—big time.
In order to save a few bucks (i.e., beer money) I told our painter that we'd clean up after he finished. No big deal, just some paper on the floors and plastic on the windows. Oh yeah. Nancy and I spent most of today (Thursday) pulling down plastic, pulling staples and ripping up paper. Interestingly, the thin Kraft paper that Franks daughter laid down to protect the floor did a pretty good job where it stayed down or in place. After a few coats of paint dried on it, the paper was more like a thin tarp. This made it easy to just fold it up into reasonable size bundles and load up the trailer for another dump run. We put the 14 empty paint pails (5 gals) in the trailer, but I discovered that its rated as recyclable so I'll try to unload that stuff for free. Now the shop vac is coming out for a final cleanup before the flooring gets delivered next week. By the way, that shop vac is the 5 HP, 10 gal one I bought from Sears to remodel the Denver house in 1976. 33 years old, butt ugly, but it still sucks—big time.
Wednesday, November 4, 2009
Exterior Complete (Day 374)
The Architectural Committee met today and reviewed our case. We've been on their minds for a year now and I'm sure they want to clear our case from the docket. Our representative (aka task master) on the committee dropped by at 9:58 am to review our progress so they could make a decision on our case at the 10 am meeting. You can see that the house got a lot of scrutiny. He walked around the front yard asked few questions and said it looked good and he'd recommend that we be considered complete and get our refund (half of the $1000 deposit). The other half goes for cocktail parties I presume. Anyway, all that work and a two-minute review. Case closed.
Even though we're done, we not really finished. I started to put up the exterior lights and learned a lesson about Chinese lighting fixtures. Their mounting brackets don't go onto an American style recessed box, so some drilling and mods have to be made. This is the sort of thing that would add a day to the electrican's bill and $500 to the cost of the lights. So off to the hardware store for a abrasive bit, some washers, and different screws. Should have them all up tomorrow if the rain holds off.
Frank the drywaller finished shooting the topcoat on the main house today. Actually, his daughter Jessica did the painting and Frank did the back rolling. 2 hours to paint about 12,000 square feet of wall and ceiling with 25 gals of latex (Home Depot Premium Plus). It looks pretty good, but now we need to strip all masked windows, skylights and doors, and remove the paper from the floor. That should go pretty fast, then some cleaning up and the house will look sort of finished inside.
Craig Wallin, our former neighbor in KP and my building mentor, will be happy to know that we bought a slug of cabinets from Discount Cabinets of Washington (Sequim, WA) for the butlers pantry and mudroom. Steve and Jere are quite a pair: they sort of remind me of the Bob and Ray show on PBS. Jere is the color guy and Steve is the measure, design, and price guy. We'd had a first estimate from them about 2 weeks ago, but it was a bit rich for our rapidly diminishing budget. So we called them back and made some simplifications. Eliminated 4 cabinets and a large bookshelf, which I'll build myself. The pantry cabinets are Omega (brand) all plywood with stained Cherry frames and doors (Shaker style). The mudroom cabinets are the same but with a burgundy stain to match the kitchen cabinets±. They should be ready and delivered about mid December in exchange for the second half of the invoice. Looks like I need to find another consulting gig and Nancy needs to double up on her hours for the Xmas season.
Even though we're done, we not really finished. I started to put up the exterior lights and learned a lesson about Chinese lighting fixtures. Their mounting brackets don't go onto an American style recessed box, so some drilling and mods have to be made. This is the sort of thing that would add a day to the electrican's bill and $500 to the cost of the lights. So off to the hardware store for a abrasive bit, some washers, and different screws. Should have them all up tomorrow if the rain holds off.
Frank the drywaller finished shooting the topcoat on the main house today. Actually, his daughter Jessica did the painting and Frank did the back rolling. 2 hours to paint about 12,000 square feet of wall and ceiling with 25 gals of latex (Home Depot Premium Plus). It looks pretty good, but now we need to strip all masked windows, skylights and doors, and remove the paper from the floor. That should go pretty fast, then some cleaning up and the house will look sort of finished inside.
Craig Wallin, our former neighbor in KP and my building mentor, will be happy to know that we bought a slug of cabinets from Discount Cabinets of Washington (Sequim, WA) for the butlers pantry and mudroom. Steve and Jere are quite a pair: they sort of remind me of the Bob and Ray show on PBS. Jere is the color guy and Steve is the measure, design, and price guy. We'd had a first estimate from them about 2 weeks ago, but it was a bit rich for our rapidly diminishing budget. So we called them back and made some simplifications. Eliminated 4 cabinets and a large bookshelf, which I'll build myself. The pantry cabinets are Omega (brand) all plywood with stained Cherry frames and doors (Shaker style). The mudroom cabinets are the same but with a burgundy stain to match the kitchen cabinets±. They should be ready and delivered about mid December in exchange for the second half of the invoice. Looks like I need to find another consulting gig and Nancy needs to double up on her hours for the Xmas season.
Subscribe to:
Posts (Atom)
Subcontractors and Suppliers
- Balco Excav. (land clearing, Bill Snyder)
- Bill McCutchen's Mill (cedar trim)
- Blake Tile and Stone, Sequim (Judy Reno, Eldorado Stone, Tile)
- Bob Brown Plumbing (Bob & Josh Brown)
- Boise Cascade joists (from Carls)
- Carl's Building Supply (Mike, Melissa, Michele, Terry & Lawrence)
- Castlerock Landscaping (Tim Hamm, Sequim)
- Cotton RediMix (concrete and gravel)
- Craighead Electric (Gary Estes)
- Custom Hearth (propane fireplaces), Pousbo
- Daltile (Seattle, Wedi board)
- Discount Cabinets of Washington (Sequim)
- Discovery Bay Materials (gravel, top soil)
- Earl Kong (professional forester, PT))
- EcoHaus (Amer. Clay Plaster, cork flooring)
- Ellis Construction (Gary and Troy Ellis, framing)
- Evergreen Products (Drywall, Sequim)
- Fergusons, Seattle (Plumbing fixtures, Bud Allen Wright)
- FInlandia Saunas (Tigard, OR)
- Fitzgerald Concrete (driveway, Mike Fitzgerald)
- Four Corners Nursery (trees, Port Hadlock)
- Frank Feltes Custom Drywall and Painting (drywall and painting)
- Frank Ward and Wayne Jobst (Stone masons)
- Fredricks Appliances (Redmond, all appliances)
- Giraffe Gutters (Dan Shaw, Chimicum)
- Glass Etchings by Perrett (Jerry Perrett)
- Hadlock Building Supply (bits and pieces)
- Hardiboard, siding, backer board (from Carls and Home Depot)
- Henerys Hardware (Cabot stain, misc. fasteners)
- Hi-Tech Electronics (Audio & Media, Port Angeles)
- Hide-A-Hose (Joseph, A-B Vacuum, Puyallup, WA)
- Home Depot (electrical & plumbing supplies, interior paint)
- Home Storage Solutions (John Plake, PT)
- Hope Roofing (Pabco Paramont Advantage shingles)
- Jim's Tool Time (J. Quandt, misc. carpentry)
- K&D Concrete (Don McNeese)
- Kitchen and Bath Studio (Shelly Little, cabinets)
- Levi's Energy Services LLC (radiant design, vents, propane piping)
- Meta Marble and Granite (travertine), Seattle
- Michaelangelo (sepentinite), Seattle
- Mikael Brostrom (Structural Engineer)
- Mills Interiors (wood flooring, some tile)
- North Coast Electrical (Electrical Supplies)
- Olympic Garage Doors (Sequim)
- Penisula Flooring (carpet)
- Penisula Shower and Mirror (Sequim)
- PexSupply (online plumbing and radiant supplies)
- Puget Sound Power (and Atelco installers)
- Richard Berg Architects (Richard and Darlene)
- Richard Gifford Construction (septic, dry wells and grading)
- Richerts Marble and Granite (countertop fabricators)
- Seattle Lighting (lighting fixtures)
- Secret Gardens Nursery (Sheila Piccini)
- Shine Quarry (basalt for landscaping)
- Sierra Pacific Windows (Rob Sorg)
- Simpson Doors (from Carls)
- Simpson Strong Tie (fasteners & hold downs)
- Stewart Excavating (Mark Stewart, foundation)
- Sunshine Propane (propane and tank)
- Therma-Tru Doors (from Carls)
- Tracy's Insulation (batts and blow in)
- Trex Decking (from Carls)
- Trussworks (roof trusses, Carl's)
- Velux (Skylights and Solar tubes, Carls)
- Versalam beams (from Carls)
- Warmboard (Bruce Hull)
- Wisbo Aquipex, Taco Pumps, Polaris tank (Sunshine Propane)
Followers
About Me

- Kala Point Builder
- Professional geologist (USGS, 1972-2008), amateur home remodeler and now builder. Interested in sailing, all things involving salt water, woodworking, and food in general. Owner of Paleo Seis Surveys LLC, consulting in Quaternary geology and geological hazards.