Its appearance won't change for a while, until we start the siding which is several months off. The last two photos are of the main entrance with a small porch overhang to protect the front door and the sunroom with a larger (4' x 10') porch. Just to the right is the master bedroom and the bathroom (at the back). When I finish my geology consulting job in Idaho Falls (a god awful place to be in the winter) I hope to get back to basics (plumbing and painting) this next week. I'll be in charge of turd management (offically known as plumbing waste lines) and Nancy is in charge of painting (the beautification process).
Building a House in Kala Point, Port Townsend, WA
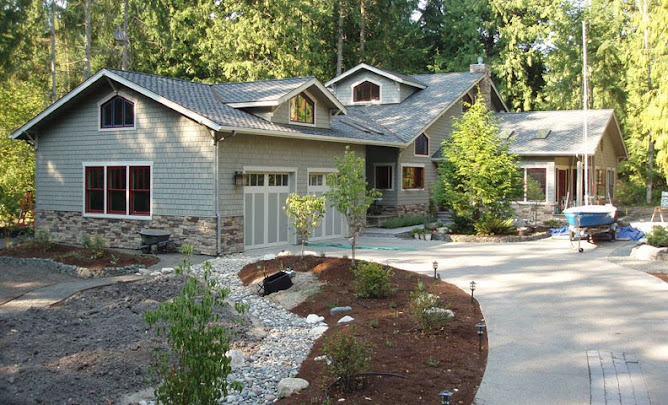
A running narrative of first-time builders of their retirement home in Port Townsend, WA (NE corner of the Olympic Pennisula, 60 miles NW of Seattle). Follow us as this adventure unfolds in late 2008 and beyond. 18 months under construction, we moved in on May 25th, 2010. Photo taken August 15, 2010.
Search This Blog
Saturday, February 28, 2009
Roof on, windows in (Day 129 of 273)
Not much to report this week except the roof is on and the Sierra Pacific windows and doors are in. Ellis Construction has moved on to their next house, a 4000 sq. ft house in Port Ludlow (read Atheron CA or Genese CO for comparison). They'll be there for 2 months, or around May 1st. As I've mentioned before, I can't say enough good things about Gary and Troy—quality guys who work quietly, quickly, and with quality outcomes.Here are a few photos of the house.
Its appearance won't change for a while, until we start the siding which is several months off. The last two photos are of the main entrance with a small porch overhang to protect the front door and the sunroom with a larger (4' x 10') porch. Just to the right is the master bedroom and the bathroom (at the back). When I finish my geology consulting job in Idaho Falls (a god awful place to be in the winter) I hope to get back to basics (plumbing and painting) this next week. I'll be in charge of turd management (offically known as plumbing waste lines) and Nancy is in charge of painting (the beautification process).


Its appearance won't change for a while, until we start the siding which is several months off. The last two photos are of the main entrance with a small porch overhang to protect the front door and the sunroom with a larger (4' x 10') porch. Just to the right is the master bedroom and the bathroom (at the back). When I finish my geology consulting job in Idaho Falls (a god awful place to be in the winter) I hope to get back to basics (plumbing and painting) this next week. I'll be in charge of turd management (offically known as plumbing waste lines) and Nancy is in charge of painting (the beautification process).
Saturday, February 21, 2009
Windows going in, roof going on (Day 123 of 273)
This past week has been pretty busy at the house site. Gary and Troy (Ellis Construction) were finishing off various internal walls that were left for later (when they focused on drying in the house), and putting the skylights in. The roofers had the shingles loaded to the roof, all 20,000 pounds of it.
That brought back memories of our roofer in Denver, Peter Douglas of Convenant Roofing (Ann, there's the name you need). Peter worked mainly alone and didn't get things done as fast as most crews. So he ordered the shingles and they came before the rip off was done. The delivery guys asked me where to put the shingles, so on the ground they went (at least they were in the back yard). So for the next three weeks, Peter hauled bundles of shingles up and onto our 12:12 roof in Denver. Talk about a mule; never complained a bit and typically was signing show tunes when he was roofing. But I digress.
The roofers started nailing on Wednesday, after using a propane blowtorch to melt the frost on the roof. They laid about 600 square ft (of 4000) and all the valley flashing. On Thursday, when I arrived they were onto the back of the house but took off at noon. Friday was the same way. So I asked their supervisor what was going on. He said they'd cut back on staff and eliminated overtime, so the crew only had enough hours left to work half days on Thursday and Friday. Monday will be a new pay period, so I expect that they'll be done roofing by next Tuesday night, which means the job will have taken a week for 3 guys. Not bad considering how heavy and stiff these shingles are. And did I mention the roof looks great and we love the color.


On Thursday and Friday, Gary and Troy started installing the Sierra Pacific windows. I helped with a couple of the heavy ones, but mostly tried to stay outta the way. They had to reframe a couple of the openings since we'd made changes that weren't on the plans or were read wrong from the plans (its that 3/6 vs 36 notation thing).
I finished up the psuedo Warmboard project and ran all the piping down to the basement, so we're ready to hook up the system and pressure it a few weeks. All is well, for now. Michael as a consulting geology job for the Idaho National Laboratory in early March, we we'll have to leave the house alone and concentrate on generating a little revenue. Plumbing is the next mission, starting around March 9th. Cheers.
On Thursday and Friday, Gary and Troy started installing the Sierra Pacific windows. I helped with a couple of the heavy ones, but mostly tried to stay outta the way. They had to reframe a couple of the openings since we'd made changes that weren't on the plans or were read wrong from the plans (its that 3/6 vs 36 notation thing).
I finished up the psuedo Warmboard project and ran all the piping down to the basement, so we're ready to hook up the system and pressure it a few weeks. All is well, for now. Michael as a consulting geology job for the Idaho National Laboratory in early March, we we'll have to leave the house alone and concentrate on generating a little revenue. Plumbing is the next mission, starting around March 9th. Cheers.
Monday, February 16, 2009
Getting Laid in the Love Nest (Day 118 of 273)
Now, I know where all of your dirty little minds are right now, and that's in the wrong place. The psuedo-Warmboard is getting laid in the second story part of the house, aka the "Love Nest." 
Nancy and I sliced up about 20 sheets of 5/8" AC plywood into 11 3/8" wide strips and I've been fastening them down in a grid pattern for the Pex tubing (see Day 92 blog). With the 5/8" Pex between the strips, the Pex is on 12" centers, just like the Warmboard. I laid all 80 strips (8' long, with miscellaneous filler pieces) in about 8 hours. It was easy, but my knees took a hit (hello Dr. Advil). Today I started the custom routing of the 36 return loops (ends) and the plunge holes (where the tubing goes downstairs), which will take 6-8 hours considering how feeble carpenter is. We'll have 2 heating loops upstairs, each about 280 ft long (300 ft is the max) in a third zone for heating. We wanted to be able to heat the Love Nest when and if needed, so Levi added a third manifold and Taco pump (1/40 hp) on the basement heating panel. I also had him add temperature gauges (old analog style) for the outgoing and returning radiant fluids, since I like gauges and data (old geologists never die, they just loose their data).
Gary Ellis loaned me his standup screw gun. What a tool. It loads 50 drywall screws per plastic strip and feeds them like machine gun bullets. 20 strips and 1000 screws to a bucket. Started screwing down the aforementioned strips (11 3/8"), and drove a screw in each side every 12-16". Did the whole bucket and floor in 75 minutes, including misfires, which equates to 133 screws a minute. Not bad for an old fart. All my screwing is done for a while.
It'll take a week of part-time days to route the ends and lay and caulk the tubing, which I bought from PexSupply, currently my favorite place to spend $$ on the internet. I'm buying a Pex Expander Tool ($300) for making all the connections with the hopes of selling it used on the internet (Craigslist) or to Levi Ross, who has started his own radiant consulting business.
Nancy and I sliced up about 20 sheets of 5/8" AC plywood into 11 3/8" wide strips and I've been fastening them down in a grid pattern for the Pex tubing (see Day 92 blog). With the 5/8" Pex between the strips, the Pex is on 12" centers, just like the Warmboard. I laid all 80 strips (8' long, with miscellaneous filler pieces) in about 8 hours. It was easy, but my knees took a hit (hello Dr. Advil). Today I started the custom routing of the 36 return loops (ends) and the plunge holes (where the tubing goes downstairs), which will take 6-8 hours considering how feeble carpenter is. We'll have 2 heating loops upstairs, each about 280 ft long (300 ft is the max) in a third zone for heating. We wanted to be able to heat the Love Nest when and if needed, so Levi added a third manifold and Taco pump (1/40 hp) on the basement heating panel. I also had him add temperature gauges (old analog style) for the outgoing and returning radiant fluids, since I like gauges and data (old geologists never die, they just loose their data).
Gary Ellis loaned me his standup screw gun. What a tool. It loads 50 drywall screws per plastic strip and feeds them like machine gun bullets. 20 strips and 1000 screws to a bucket. Started screwing down the aforementioned strips (11 3/8"), and drove a screw in each side every 12-16". Did the whole bucket and floor in 75 minutes, including misfires, which equates to 133 screws a minute. Not bad for an old fart. All my screwing is done for a while.
It'll take a week of part-time days to route the ends and lay and caulk the tubing, which I bought from PexSupply, currently my favorite place to spend $$ on the internet. I'm buying a Pex Expander Tool ($300) for making all the connections with the hopes of selling it used on the internet (Craigslist) or to Levi Ross, who has started his own radiant consulting business.
Saturday, February 14, 2009
Putting a wrap on it (Day 116 of 273, Valentines Day)

Saturday, February 7, 2009
Roofing bid accepted (Day 109 of 273)
Once the committee made a decision to accept our roofing choice, we needed to select a roofing company. You'd think that this is straightforward, but not always. In Denver the least expensive roofing estimate we got for the old house was about $7500, and the most expensive (of 5 bid) was about $13,500. All the same materials and specs, so it pays to shop around. We ended up using the $7500 guy because he was the only one the crawled all over the roof and was willing to discuss the job in detail. Other than being a bit slow and singing show tunes on the rooftop, we were entirely satisfied with Peter Douglas (Covenant Roofing). Now that house had 2500 sq ft of roofing on a 12:12 pitch and one dormer. It was a complete tear off and redeck, and used 30 yr shingles (not the best, but pretty good for the purpose of resale).
On the new house we have about 4200 sq. ft of roofing at a 5:12 pitch (much easier to climb on). The underlayment (#30 tar paper) is already done ($1500), so the bids we got were for the Pabco Paramont Advantage (TL, 50 yr, 495#/sq.), with is comparable with the GAF Grand Canyon and CertainTeed Presidential TL shingles. The bids included all valley flashing (24" metal), sidewall flashing, and installation of the roof jacks (vents), exhaust vents, and skylights (9).
Our preferred roofer came in high, as he predicted so this presented a bit of a dilemma because we really liked the guy (Eric). He'd said that he had never got a roofing job in Kala Point because he was too expensive (compounded with the shingle cost). Eric bid about $17,800 for the job.
The second most expensive bid came from another likable guy, Joe Bartlett of Port Ludlow, a tony little village down the water. Boats, seaplanes and retired executives come to mind. Bartlett bid $15,124 and might have come down $100 because he overestimated the number of skylights by one. No matter, he was outbid by two others.
The second least expensive bid came from some guys in Port Orchard, down near Bremerton. C&M Construction (Cloise and Mike). They prepared a very complete estimate and had good refs (voted N. 1 contractor in S. Kitsap for 2008; but who voted?). Anyway they came in at $13,517, a pretty good price.
The least expensive bid was from the local, big-dog roofing company, Hope Roofing. I had figured they'd be high (big building, lots of employees, etc.), but they weren't. I wanted to use a local company to keep our bucks in the area. At first the bid of $13,192 was the low one, but then I noticed (yes, read the fine print) that they wanted an additional $125 for flashing of each skylight and chimney. At 9+1, that amounted to $1250 (+tax = a total of $1355) which pushed the real estimate up to $14,547. I found the additional amount unwarranted, since we purposely selected Velux QFS skylights, which are self-flashing and very easy to roof on top of. So, Steve Ford waived the skylight flashing cost and we settled for the original low bid of $13,192.
Assuming that they install 42 squares of roofing, the cost will be $314 per square. Add on the $36 per square cost for the underlayment, and we netted out at $350 per square. Sounds like a hell of a lot of money to keep rain off your heads, but the Denver house came out at $300 per square with the tear off and a much lesser grade shingle (ca. half the cost).
So if you're looking to roof or reroof in the near future, these numbers should help. Roofers are a bit hungry right now (they all came right out and got bids to me in a few days), and shingle prices are steady, not increasing like last summer (remember that asphalt is the dregs in the petroleum distillate chain and oil was @ $140 bbl). I suspect that we could roof a new house outside of Kala Point for about $250/square with a good double-layer shingle (GAF Sequoia or Presidental, or Pabco Paramont). We'll call that additional $100 a square (or $4200) one of the costs of living in a lovely, but covenant-controlled community. We could have opted for wooden shingles or cement tiles at $25,000+, or slate at $75,000-$100,000, but then we wouldn't be having any kitchen appliances and Nancy would be a widow.
On the new house we have about 4200 sq. ft of roofing at a 5:12 pitch (much easier to climb on). The underlayment (#30 tar paper) is already done ($1500), so the bids we got were for the Pabco Paramont Advantage (TL, 50 yr, 495#/sq.), with is comparable with the GAF Grand Canyon and CertainTeed Presidential TL shingles. The bids included all valley flashing (24" metal), sidewall flashing, and installation of the roof jacks (vents), exhaust vents, and skylights (9).

The second most expensive bid came from another likable guy, Joe Bartlett of Port Ludlow, a tony little village down the water. Boats, seaplanes and retired executives come to mind. Bartlett bid $15,124 and might have come down $100 because he overestimated the number of skylights by one. No matter, he was outbid by two others.
The second least expensive bid came from some guys in Port Orchard, down near Bremerton. C&M Construction (Cloise and Mike). They prepared a very complete estimate and had good refs (voted N. 1 contractor in S. Kitsap for 2008; but who voted?). Anyway they came in at $13,517, a pretty good price.
The least expensive bid was from the local, big-dog roofing company, Hope Roofing. I had figured they'd be high (big building, lots of employees, etc.), but they weren't. I wanted to use a local company to keep our bucks in the area. At first the bid of $13,192 was the low one, but then I noticed (yes, read the fine print) that they wanted an additional $125 for flashing of each skylight and chimney. At 9+1, that amounted to $1250 (+tax = a total of $1355) which pushed the real estimate up to $14,547. I found the additional amount unwarranted, since we purposely selected Velux QFS skylights, which are self-flashing and very easy to roof on top of. So, Steve Ford waived the skylight flashing cost and we settled for the original low bid of $13,192.
Assuming that they install 42 squares of roofing, the cost will be $314 per square. Add on the $36 per square cost for the underlayment, and we netted out at $350 per square. Sounds like a hell of a lot of money to keep rain off your heads, but the Denver house came out at $300 per square with the tear off and a much lesser grade shingle (ca. half the cost).
So if you're looking to roof or reroof in the near future, these numbers should help. Roofers are a bit hungry right now (they all came right out and got bids to me in a few days), and shingle prices are steady, not increasing like last summer (remember that asphalt is the dregs in the petroleum distillate chain and oil was @ $140 bbl). I suspect that we could roof a new house outside of Kala Point for about $250/square with a good double-layer shingle (GAF Sequoia or Presidental, or Pabco Paramont). We'll call that additional $100 a square (or $4200) one of the costs of living in a lovely, but covenant-controlled community. We could have opted for wooden shingles or cement tiles at $25,000+, or slate at $75,000-$100,000, but then we wouldn't be having any kitchen appliances and Nancy would be a widow.
Thursday, February 5, 2009
Cedar Mill running (Day 107 of 273)
Boy, what a nice day. The sun is out and the thermo broke 55°F Wed. afternoon; warmest day since Thanksgiving. Nancy and I wandered down to Bill McCutchen's saw mill (see previous post, Day 98) to watch him cut the raw wood for our
trim. In exchange for felling a dozen large cedars from a neighbors lot (clearing for future house), he gets the wood for our job. I took a bunch of pictures
for the Mr. Bills (the wood cutter and my father-in-law). Wood doesn't get any fresher than this, smells great and looks good. The process is as follows. He drags a log (up to 21 ft long and 34" diameter) to the side of the mill, and the mill lifts it up onto the bed. He levels the log with hydraulic lifts so its center line is parallel to the cutting plane, then has at it. The bark comes off first, then 1x slices until he is down to solid wood. He was getting 12" x 20' slices from this log. After the log is trued up on all four sides, he starts cutting 5/4 (1.25") slabs.
This will be dried and ripped to the proper size. We need some 8", 6", and a ton of 4" for door and window trim, as well as 1x6 T&G (tongue and groove) for the soffit. I suspect we'll end up buying about $2000 of cedar trim for the house, which will save us $450 over Carl's prices, and we're even buying local. One extra thing to mention. When all the windows and exterior doors are installed, Bill will come over, measure all the windows and doors, and cut the trim to size in his shop. That way he'll make the best use of the wood, and we'll only pay for what he delivers. I figure that this little freebie will save me a week of trim cutting.



Monday, February 2, 2009
Dancing with the Roof Divas (Day 104 of 273)
I knew it was too good—two weeks of dry weather and we're about ready to get "dried in". Eric (potential roofer) put tar paper (30#) on the main house and second floor, and will complete the job on the weekend after Gary gets the garage and mudroom/sauna roof decking on. Eric mentioned that there was a new roofing material that we might look at since it is easier (read less expensive) to put down owing to a new layout pattern, yet it meets the stringent TL requirements of the Kala Point Architectural Committee (lots of retired guys without much to do I guess). We're OK with the idea of a committee, it keeps the houses from looking like they belong in the Berkeley Hills.
So last fall we had to decide on the brand and color of our roofing when we submitted our permit to the committee. We had two choices of asphalt composition roofing: GAF Grand Canyon ($185 and 450# per square) and Certainteed Presidental TL (similar price). The TL is the give-away term, which I've just realized. TL = triple laminate. They really want everyone to have a classic wooden shake roof, but times are changing and these roofs are a known fire threat. So they've allowed "shake like" roofs that have a lot of relief (topographic, not monetary). There is a metal roof with a shake-like appearance and granules, but it looks like dog and is expensive. There is cement tile shake, but its heavier and monotonous. Most owners are going to the TL asphalt shingles. Another key term in the roofing requirements is "earth tone." Now, being a geologist all my career in the SW US, I know what earth tones are: browns, grays, some reds, etc. Not green (flora) or blue (sky). Their idea of earth tone is black or brownish black or grayish black; specifically nothing with green, blue, or reds. Slate is probably OK (but it has all the aforementioned colors) since it cost an arm and a leg, but we won't even do there. So I see a battle ahead.
We filed an amendment to our building application with the committee, and they'll hear it at their monthly meeting tomorrow (Wed.). We're asking for Pabco (brand) Paramont Advantage (model) in Driftwood or (the dreaded) Antique black. Runs about $135 and 495# a square (110 ft2), so its a bit cheaper and a bit heavier. Eric estimates that the labor will be 2/3rds as much as for the two accepted brands owing to the layout pattern. I think the black is a no-brainer for them, but driftwood (browish gray) is a bit touchy. Maybe they need to drive across about 100 miles of Mancos shale (yes Tuttle) in the 4 Corners area to see what an earth tone really is. I figured the Driftwood color would grab them by the cojones, seeing as we have tons of it down at the Kala Point beach. Then again, we're not building a beach house so that's probably a weak argument. Jeff Knott (of driftwood fame), we need your debating skills out here.
Anyway, if they don't have a quorum for the meeting tomorrow no decision will be rendered (as they do with fat), so this could go on for a while. Meanwhile, I'd like to make hay (or roof) while the sun shines. Say tuned for Machette versus the Roof Devils—Chapter 2, then Chapter 3—The Pacific Northwest Monsoon Season Arrives.
P.S. We attended the Arch. Committee meeting this morning (always a good thing to do) and after some jostling, they agreed to the Pabco shingles and the Pewter Gray color, which was about half way between the Black and Driftwood colors that we had suggested. So it was a compromise, all in the spirit of the new Obama administration (just think of the committee as the Republicans and us as the Democrats and the roofing as a $13k miniversion of the $1,000,0000,000 spending-stimulus package.) One more roofing bid and we're ready to pick a subcontractor and roof away.
So last fall we had to decide on the brand and color of our roofing when we submitted our permit to the committee. We had two choices of asphalt composition roofing: GAF Grand Canyon ($185 and 450# per square) and Certainteed Presidental TL (similar price). The TL is the give-away term, which I've just realized. TL = triple laminate. They really want everyone to have a classic wooden shake roof, but times are changing and these roofs are a known fire threat. So they've allowed "shake like" roofs that have a lot of relief (topographic, not monetary). There is a metal roof with a shake-like appearance and granules, but it looks like dog and is expensive. There is cement tile shake, but its heavier and monotonous. Most owners are going to the TL asphalt shingles. Another key term in the roofing requirements is "earth tone." Now, being a geologist all my career in the SW US, I know what earth tones are: browns, grays, some reds, etc. Not green (flora) or blue (sky). Their idea of earth tone is black or brownish black or grayish black; specifically nothing with green, blue, or reds. Slate is probably OK (but it has all the aforementioned colors) since it cost an arm and a leg, but we won't even do there. So I see a battle ahead.
We filed an amendment to our building application with the committee, and they'll hear it at their monthly meeting tomorrow (Wed.). We're asking for Pabco (brand) Paramont Advantage (model) in Driftwood or (the dreaded) Antique black. Runs about $135 and 495# a square (110 ft2), so its a bit cheaper and a bit heavier. Eric estimates that the labor will be 2/3rds as much as for the two accepted brands owing to the layout pattern. I think the black is a no-brainer for them, but driftwood (browish gray) is a bit touchy. Maybe they need to drive across about 100 miles of Mancos shale (yes Tuttle) in the 4 Corners area to see what an earth tone really is. I figured the Driftwood color would grab them by the cojones, seeing as we have tons of it down at the Kala Point beach. Then again, we're not building a beach house so that's probably a weak argument. Jeff Knott (of driftwood fame), we need your debating skills out here.
Anyway, if they don't have a quorum for the meeting tomorrow no decision will be rendered (as they do with fat), so this could go on for a while. Meanwhile, I'd like to make hay (or roof) while the sun shines. Say tuned for Machette versus the Roof Devils—Chapter 2, then Chapter 3—The Pacific Northwest Monsoon Season Arrives.
P.S. We attended the Arch. Committee meeting this morning (always a good thing to do) and after some jostling, they agreed to the Pabco shingles and the Pewter Gray color, which was about half way between the Black and Driftwood colors that we had suggested. So it was a compromise, all in the spirit of the new Obama administration (just think of the committee as the Republicans and us as the Democrats and the roofing as a $13k miniversion of the $1,000,0000,000 spending-stimulus package.) One more roofing bid and we're ready to pick a subcontractor and roof away.
Subscribe to:
Posts (Atom)
Blog Archive
-
▼
2009
(91)
-
▼
February
(7)
- Roof on, windows in (Day 129 of 273)
- Windows going in, roof going on (Day 123 of 273)
- Getting Laid in the Love Nest (Day 118 of 273)
- Putting a wrap on it (Day 116 of 273, Valentines Day)
- Roofing bid accepted (Day 109 of 273)
- Cedar Mill running (Day 107 of 273)
- Dancing with the Roof Divas (Day 104 of 273)
-
▼
February
(7)
Subcontractors and Suppliers
- Balco Excav. (land clearing, Bill Snyder)
- Bill McCutchen's Mill (cedar trim)
- Blake Tile and Stone, Sequim (Judy Reno, Eldorado Stone, Tile)
- Bob Brown Plumbing (Bob & Josh Brown)
- Boise Cascade joists (from Carls)
- Carl's Building Supply (Mike, Melissa, Michele, Terry & Lawrence)
- Castlerock Landscaping (Tim Hamm, Sequim)
- Cotton RediMix (concrete and gravel)
- Craighead Electric (Gary Estes)
- Custom Hearth (propane fireplaces), Pousbo
- Daltile (Seattle, Wedi board)
- Discount Cabinets of Washington (Sequim)
- Discovery Bay Materials (gravel, top soil)
- Earl Kong (professional forester, PT))
- EcoHaus (Amer. Clay Plaster, cork flooring)
- Ellis Construction (Gary and Troy Ellis, framing)
- Evergreen Products (Drywall, Sequim)
- Fergusons, Seattle (Plumbing fixtures, Bud Allen Wright)
- FInlandia Saunas (Tigard, OR)
- Fitzgerald Concrete (driveway, Mike Fitzgerald)
- Four Corners Nursery (trees, Port Hadlock)
- Frank Feltes Custom Drywall and Painting (drywall and painting)
- Frank Ward and Wayne Jobst (Stone masons)
- Fredricks Appliances (Redmond, all appliances)
- Giraffe Gutters (Dan Shaw, Chimicum)
- Glass Etchings by Perrett (Jerry Perrett)
- Hadlock Building Supply (bits and pieces)
- Hardiboard, siding, backer board (from Carls and Home Depot)
- Henerys Hardware (Cabot stain, misc. fasteners)
- Hi-Tech Electronics (Audio & Media, Port Angeles)
- Hide-A-Hose (Joseph, A-B Vacuum, Puyallup, WA)
- Home Depot (electrical & plumbing supplies, interior paint)
- Home Storage Solutions (John Plake, PT)
- Hope Roofing (Pabco Paramont Advantage shingles)
- Jim's Tool Time (J. Quandt, misc. carpentry)
- K&D Concrete (Don McNeese)
- Kitchen and Bath Studio (Shelly Little, cabinets)
- Levi's Energy Services LLC (radiant design, vents, propane piping)
- Meta Marble and Granite (travertine), Seattle
- Michaelangelo (sepentinite), Seattle
- Mikael Brostrom (Structural Engineer)
- Mills Interiors (wood flooring, some tile)
- North Coast Electrical (Electrical Supplies)
- Olympic Garage Doors (Sequim)
- Penisula Flooring (carpet)
- Penisula Shower and Mirror (Sequim)
- PexSupply (online plumbing and radiant supplies)
- Puget Sound Power (and Atelco installers)
- Richard Berg Architects (Richard and Darlene)
- Richard Gifford Construction (septic, dry wells and grading)
- Richerts Marble and Granite (countertop fabricators)
- Seattle Lighting (lighting fixtures)
- Secret Gardens Nursery (Sheila Piccini)
- Shine Quarry (basalt for landscaping)
- Sierra Pacific Windows (Rob Sorg)
- Simpson Doors (from Carls)
- Simpson Strong Tie (fasteners & hold downs)
- Stewart Excavating (Mark Stewart, foundation)
- Sunshine Propane (propane and tank)
- Therma-Tru Doors (from Carls)
- Tracy's Insulation (batts and blow in)
- Trex Decking (from Carls)
- Trussworks (roof trusses, Carl's)
- Velux (Skylights and Solar tubes, Carls)
- Versalam beams (from Carls)
- Warmboard (Bruce Hull)
- Wisbo Aquipex, Taco Pumps, Polaris tank (Sunshine Propane)
Followers
About Me

- Kala Point Builder
- Professional geologist (USGS, 1972-2008), amateur home remodeler and now builder. Interested in sailing, all things involving salt water, woodworking, and food in general. Owner of Paleo Seis Surveys LLC, consulting in Quaternary geology and geological hazards.