In any right triangle, the area of the square whose side C is the hypotenuse (the side opposite the right angle) is equal to the sum of the areas of the squares whose sides A & B are the two legs (the two sides that meet at a right angle); hence AxA + BxB = CxC.
Knowing just that and with a calculator in hand, you can layout entire house in about an hour. Now I know why I liked algegra and geometry so much.
This morning, Don (the cement guy) and I laid out the foundation outline for the house. We set the garage corner in 74' from the front and 13' from the north edge as per our Architect's plans, and let the rest fall where it may. The 13' setback will allow a 2 ft overhang for the roof and gutter, and a bit of breathing room. As it is, the house will straddle a low ridge in the rear center of the lot (see parcel 965000169 at http://maps.co.jefferson.wa.us/Website/mspub/viewer.htm?mapset=parcels_outside). A little cut here, a little fill there, and all is well.
About the time we had finished, Mark Stewart (Stewart Excavating) called and wanted to know if we could push the job up a day—OK. So Friday am the dirt flies. Tony, want to come out and log the foundation, sort of for good old times sake?
Building a House in Kala Point, Port Townsend, WA
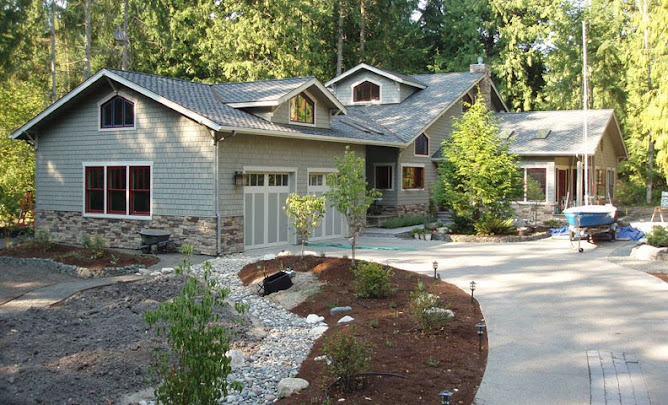
A running narrative of first-time builders of their retirement home in Port Townsend, WA (NE corner of the Olympic Pennisula, 60 miles NW of Seattle). Follow us as this adventure unfolds in late 2008 and beyond. 18 months under construction, we moved in on May 25th, 2010. Photo taken August 15, 2010.
Search This Blog
Thursday, October 30, 2008
Tuesday, October 28, 2008
Oh boy, a big hole in the ground (Day 3 of 273)
Well, we just committed to putting a big hole in the Vashon Till (ca. 15,000 yrs old, glacial till that was overridden by 1,000 m of ice). Its a gravelly silty sand (USGS analysis) with clasts as much as 30-40 cm (1.2-1.4 ft) in diameter. Light gray, unstratified, and hard to dig owing to all the prior icy overburden. Although there is now sign of it, I have a side bet with the concrete guy about clay--he says we'll hit some, and I don't see any reason why. Should be a interesting if he's right.
Anyway, the excavating is about half the total cost ($6200) and the other half is hauling away 300 cubic yards of material to some unknown destination (another hole, probably). You say, just what is 300 cubic yards? Well, think of a layer 1 ft thick, 10 ft wide, and 900 ft long (a nice long road base).
A large backhoe is supposed to arrive on Monday and have at it. By Monday night, the basement should be dug and the spoils removed. On Tuesday, about 400 cubic yards will come out of the two crawl spaces; half will go out front for a long, wide berm and the other half will be used to backfill around the foundation at the end of November. Hopefully my math will work out; extra haulage is about $10/yd and those yards pile up quickly. Cement guys arrive Wed., Nov. 5 to survey in the footers. Mrs Obama should be measuring for drapes that morning. Oh boy, we're having fun now.
Here are a few pictures of the site after clearing and house layout. Nancy, all 5'2" of her is in both pictures. The second one shows the two cedars and huckleberry bush that we managed to save, near the entrance to the house. Dirt flies tomorrow (Friday).

Anyway, the excavating is about half the total cost ($6200) and the other half is hauling away 300 cubic yards of material to some unknown destination (another hole, probably). You say, just what is 300 cubic yards? Well, think of a layer 1 ft thick, 10 ft wide, and 900 ft long (a nice long road base).
A large backhoe is supposed to arrive on Monday and have at it. By Monday night, the basement should be dug and the spoils removed. On Tuesday, about 400 cubic yards will come out of the two crawl spaces; half will go out front for a long, wide berm and the other half will be used to backfill around the foundation at the end of November. Hopefully my math will work out; extra haulage is about $10/yd and those yards pile up quickly. Cement guys arrive Wed., Nov. 5 to survey in the footers. Mrs Obama should be measuring for drapes that morning. Oh boy, we're having fun now.
Here are a few pictures of the site after clearing and house layout. Nancy, all 5'2" of her is in both pictures. The second one shows the two cedars and huckleberry bush that we managed to save, near the entrance to the house. Dirt flies tomorrow (Friday).


Sunday, October 26, 2008
Ducks in a row (Day 2 of 273)
Now that the trees are falling, we need to think about all the stuff that has to be purchased in the next few months. First off is the lumber package (framing) and Warmboard radiant subfloor (http://www.warmboard.com/). We choose this heating system for its simplicity and comfort. Warm water (ca. 110-120°F) flows through PEX tubing that is embedded in the top of the 1 1/8" thick subfloor, which is made of plywood with an aluminum top sheet. They look like 4' x 8' logos, and cost about as much per square inch. At 100 pounds each, you don't just move them around willy-nilly. Terry at Carls is willing to take delivery from the factory, then reload them and deliver to the job site. Warmboard did the design layout for the sheets, tubing and controlled zones and sent the CAD drawings to me and our architect last June, so all we need to do now is push the button and write the check (ca. $13,000 with shipping from Portland). Shipment is 7-10 days after payment, so we are scheduled to delivery around November 28th.
One critical element of using this system is to stick to 4 ft nominal dimensions for the floor plan, thereby minimizing waste of the Warmboard sheets. We'll use it for the entire first floor (except sauna), but use electric space heating upstairs (sorry visitors, but this will help keep the nightly rental rates low).
We sent a complete set of drawings (architectural, 18 sheets; structural 14 sheets) to the local lumber yard (Carls) for take offs. They farm this out to a firm that specializes in making a comprehensive materials lists, including trusses and fasteners. Mike at Calrs uses the material list and comes with an estimate, which we hope will come in at about $45k (framers guess). Carls buys a lot of Canadian lumber and their dollar is down big time right now, so maybe we'll make budget on the wood. Carls will deliver the lumber in staged packages, which sure beats getting it all at once and letting much of it sit out in the weather. Melissa (the Window and Door expert at Carls) told me they'd deliver just about anything I need, down to a $5 buck item if it was on the way to a larger job. (see photo: Mike on the left, Melissa in the middle, and Terry on the right).

No problem there, maybe they'd bring Mexican food for lunch with the sill plates. So first we'll get the subfloor joists (engineered 11.5" BCI trusses) and Warmboard delivered after the stem walls have cured (7 days yields ca 50% of max. strength). After the subfloor is constructed, we'll have a flat/level stage to build the house on.
Windows need to arrive by the time the house is dried in (sheathed exterior and roof). This should be in mid January ±, so we have nearly two months to get them to the site. Based on we've chosen Sierra Pacific Windows and Doors of northern Califoria (www.sierrapacificwindows.com) for all exterior applications. We worked with Rob Sorg in Denver during the past year, so all the decisions are made and we just need to push the "buy" buttion and send a check for $20k. Sounds like a lot (it is), but this includes 32 window units and 2 french doors (one double and one single). They are solid wood, mainly fir (for clear finish), clad with aluminum on th outside, and have a Harvest Cranberry powder finish. Works out to about $500 a window on average. Sierra Pacific will come out after installation and inspect for warranty, then return at the end and install all the opening and locking hardware. In addition, I'm working up the skylight order, which is with Velux. They will be nine stationary units and one Solartube (sauna). We might buy these through Home Depot since they have the best prices on standard size units, but they don't have all the ones we want and I've had trouble with damaged units on delivery (in Denver).
Doors come next, and they don't give them away. We'll probably use Simpson solid fir doors (shaker style) for a northwestern look on the main living area. We'll save some bucks by using paint grade (hemlock) doors (same style) in the bedroom, baths, and pantry/laundry, and upstairs (again, the rent issue). Eight of the 23 doors will have full glass panels to let the light bounce around the house. For the exterior, we'll use fiberglass clad doors for ease of maintenance. They can be stained, so they'll look like fir from a distance. We need a couple fire-rated doors for the garage and basement, but hope to stick with the same style that will run through the house. Doors don't need to show up for about 6 months, so no worries here. We'll continue to research options for saving some bucks; Melissa at Carls has been a great help. Looks and sounds for the all world like Amanda Ruleman, a friend of ours in Evergreen, CO (Amanda, are you missing a twin sister?).
Nancy has started on cabinet reconnaissance. We need 24 linear ft of cabinet (full lower and half upper) with refrigerator and double oven cases. The free-standing island will have cabinets below (no real design yet), and it is 3/6 by 6/0. We are looking at shaker-style natural finish cherry. We have 3 bids so far.
1) Jesse Bay cabinets in Port Angeles is owned by a nice 40-yr-old guy we met at the Seattle Home Show last year. Its a small shop, much like the one Bill Hart (Nancy's dad) worked for in the Bay Area back when. They'll make a quality custom cabinet, but are the most expensive so far (ca. $22). Solid plywood boxes, hardwood face frames and doors, and tongue and groove construction on drawers.
2) The second bid was from Bleimeister Cabinets in Sequim. They buy pre-made MDF boxes (maple finish) and solid wood doors, and do all the custom fitting in their shop. They came in at about $15k, but are the lowest grade cabinets of the three.
3) The third bid is by the Kitchen and Bath Store (Shelley Little) in Port Townsend. We like her and her attention to detail; lots of suggestions for efficient usage of space. Their Medallion brand cabinets are between the others in quality, but they have some more attractive door options than the others. Including upgrades for custom door style and plywood boxes, they came in at about $20k, and are willing to discount it a bit to us as "builders". Hopefully, we can drag Bill and June Hart up to see Port Townsend next summer and have him supervise the cabinet installation by the General Contractor.
We'll cast around a bit more, but we're favoring choice #3 for now. Appliances are another story and entirely in Nancy's control, but early estimates are between $12-15k for a 30" Wolf gas (propane) 6-burner rangetop, a 30" electric double oven, stainless steel French (3) door refrigerator, Bosch dishwasher, and 30" high-volume range hood. No one seems to be willing to deal much on the high-end appliances: the manufacturers seem to be able to control any discounting from the MRSP. They don't seem to realize that the US and everyone else in going into an extended recession. PS, rumor has it that GE is getting out of the appliance business. Seems appropriate considering all the trouble we've had with the 4-yr old one in our rental house, but that's another story.
One critical element of using this system is to stick to 4 ft nominal dimensions for the floor plan, thereby minimizing waste of the Warmboard sheets. We'll use it for the entire first floor (except sauna), but use electric space heating upstairs (sorry visitors, but this will help keep the nightly rental rates low).
We sent a complete set of drawings (architectural, 18 sheets; structural 14 sheets) to the local lumber yard (Carls) for take offs. They farm this out to a firm that specializes in making a comprehensive materials lists, including trusses and fasteners. Mike at Calrs uses the material list and comes with an estimate, which we hope will come in at about $45k (framers guess). Carls buys a lot of Canadian lumber and their dollar is down big time right now, so maybe we'll make budget on the wood. Carls will deliver the lumber in staged packages, which sure beats getting it all at once and letting much of it sit out in the weather. Melissa (the Window and Door expert at Carls) told me they'd deliver just about anything I need, down to a $5 buck item if it was on the way to a larger job. (see photo: Mike on the left, Melissa in the middle, and Terry on the right).
No problem there, maybe they'd bring Mexican food for lunch with the sill plates. So first we'll get the subfloor joists (engineered 11.5" BCI trusses) and Warmboard delivered after the stem walls have cured (7 days yields ca 50% of max. strength). After the subfloor is constructed, we'll have a flat/level stage to build the house on.
Windows need to arrive by the time the house is dried in (sheathed exterior and roof). This should be in mid January ±, so we have nearly two months to get them to the site. Based on we've chosen Sierra Pacific Windows and Doors of northern Califoria (www.sierrapacificwindows.com) for all exterior applications. We worked with Rob Sorg in Denver during the past year, so all the decisions are made and we just need to push the "buy" buttion and send a check for $20k. Sounds like a lot (it is), but this includes 32 window units and 2 french doors (one double and one single). They are solid wood, mainly fir (for clear finish), clad with aluminum on th outside, and have a Harvest Cranberry powder finish. Works out to about $500 a window on average. Sierra Pacific will come out after installation and inspect for warranty, then return at the end and install all the opening and locking hardware. In addition, I'm working up the skylight order, which is with Velux. They will be nine stationary units and one Solartube (sauna). We might buy these through Home Depot since they have the best prices on standard size units, but they don't have all the ones we want and I've had trouble with damaged units on delivery (in Denver).
Doors come next, and they don't give them away. We'll probably use Simpson solid fir doors (shaker style) for a northwestern look on the main living area. We'll save some bucks by using paint grade (hemlock) doors (same style) in the bedroom, baths, and pantry/laundry, and upstairs (again, the rent issue). Eight of the 23 doors will have full glass panels to let the light bounce around the house. For the exterior, we'll use fiberglass clad doors for ease of maintenance. They can be stained, so they'll look like fir from a distance. We need a couple fire-rated doors for the garage and basement, but hope to stick with the same style that will run through the house. Doors don't need to show up for about 6 months, so no worries here. We'll continue to research options for saving some bucks; Melissa at Carls has been a great help. Looks and sounds for the all world like Amanda Ruleman, a friend of ours in Evergreen, CO (Amanda, are you missing a twin sister?).
Nancy has started on cabinet reconnaissance. We need 24 linear ft of cabinet (full lower and half upper) with refrigerator and double oven cases. The free-standing island will have cabinets below (no real design yet), and it is 3/6 by 6/0. We are looking at shaker-style natural finish cherry. We have 3 bids so far.
1) Jesse Bay cabinets in Port Angeles is owned by a nice 40-yr-old guy we met at the Seattle Home Show last year. Its a small shop, much like the one Bill Hart (Nancy's dad) worked for in the Bay Area back when. They'll make a quality custom cabinet, but are the most expensive so far (ca. $22). Solid plywood boxes, hardwood face frames and doors, and tongue and groove construction on drawers.
2) The second bid was from Bleimeister Cabinets in Sequim. They buy pre-made MDF boxes (maple finish) and solid wood doors, and do all the custom fitting in their shop. They came in at about $15k, but are the lowest grade cabinets of the three.
3) The third bid is by the Kitchen and Bath Store (Shelley Little) in Port Townsend. We like her and her attention to detail; lots of suggestions for efficient usage of space. Their Medallion brand cabinets are between the others in quality, but they have some more attractive door options than the others. Including upgrades for custom door style and plywood boxes, they came in at about $20k, and are willing to discount it a bit to us as "builders". Hopefully, we can drag Bill and June Hart up to see Port Townsend next summer and have him supervise the cabinet installation by the General Contractor.
We'll cast around a bit more, but we're favoring choice #3 for now. Appliances are another story and entirely in Nancy's control, but early estimates are between $12-15k for a 30" Wolf gas (propane) 6-burner rangetop, a 30" electric double oven, stainless steel French (3) door refrigerator, Bosch dishwasher, and 30" high-volume range hood. No one seems to be willing to deal much on the high-end appliances: the manufacturers seem to be able to control any discounting from the MRSP. They don't seem to realize that the US and everyone else in going into an extended recession. PS, rumor has it that GE is getting out of the appliance business. Seems appropriate considering all the trouble we've had with the 4-yr old one in our rental house, but that's another story.

Saturday, October 25, 2008
Timber! Then boom and crash (Day 1 of 273 to build)
Well, the trees started coming down on Thursday (Oct. 23), so that's our official start date for construction. We have 9 months (July 22nd) to get our occupancy permit and tidy up the outsides, so it doesn't look like a construction site. All went well until noon, then a little mistake occurred. The felling process for the medium-size trees (ca. 80') is to dig up their roots, then push the tree over with the backhoe (large Hitachi, 3 ft bucket; just like the kind we used for trenching faults at the USGS). Anyway, on one tree not all the roots were severed and when Bill Snyder (Balco, sub for clearing) pushed the tree it swung around and fell about 30° left of the intended direction. With a large boom, it fell across the property line and onto the neighbors backyard, taking down a fir and cedar and knocking the corner off their wood shed. To make a long story short, he removed a dead tree for them and will repair the shed. Crisis resolved (for now). 
On Friday, Joe Thompson (a semiretired, professional logger) came to fell six of the largest trees. What an impressive sight to see this guy climb a tree, chainsaw in hand. He cuts limbs on the way up, marking the trunk in 20 ft intervals, then drops the top 30-40 ft, and works his way down. The remaining 40 ft stump is then pushed over, roots attached. Then a little slicing and dicing, and you have a bunch of nice logs.
The brush is being cleared with the backhoe (overkill), shaking the dirt off and staking it in a big pile to be taken away by truck (3-4 loads, probably). In addition, we placed a culvert (12" corregated plastic, 26 ft long) beneath the intended driveway, and covered it with 1.5" crushed basalt (the local Tertiary bedrock, ca. 15 Ma) to form a mud-free entrance to the street. We'll cover the gravel with asphalt or concrete when the job is done.
So, not to bad for 2 days of de- and re-construction at the site. Hopefully, the clearing will be done by mid week, and we'll get going on a hole (ca. 600 cubic yards of dirt moving). The house plans call for a 32 ft x 26 ft full depth basement, two 26 x 22 ft crawl spaces, and the garage (30 x 26 ft) with slab on grade. All told, this amounts to ca. 600 cubic yards of dirt moving, half of which will stay on site for backfill and building long low berm at the front of the property.

On Friday, Joe Thompson (a semiretired, professional logger) came to fell six of the largest trees. What an impressive sight to see this guy climb a tree, chainsaw in hand. He cuts limbs on the way up, marking the trunk in 20 ft intervals, then drops the top 30-40 ft, and works his way down. The remaining 40 ft stump is then pushed over, roots attached. Then a little slicing and dicing, and you have a bunch of nice logs.
The brush is being cleared with the backhoe (overkill), shaking the dirt off and staking it in a big pile to be taken away by truck (3-4 loads, probably). In addition, we placed a culvert (12" corregated plastic, 26 ft long) beneath the intended driveway, and covered it with 1.5" crushed basalt (the local Tertiary bedrock, ca. 15 Ma) to form a mud-free entrance to the street. We'll cover the gravel with asphalt or concrete when the job is done.
Monday, October 13, 2008
A week off, final move from Denver
We're flying off tomorrow for Denver. We still have a van's worth of left over (keeper) stuff to move, friends to see at a farewell party, and some lingering business (MD, DDS, dinners, etc). We're staying with Zeke (Bob Fleming) in Golden for a few days then Judy and Steve Cooley (Hobie friends) for the weekend. We need to buy a egress style window well (5 ft deep, 4 ft wide), cover and ladder for the basement, which is not common out here. The prices and availability are better in Denver, so we'll throw it in with the other stuff. May buy a portable table saw from Tool King (good prices and selection, just north of the USGS on 6th Ave) in Lakewood. I'll have to rip window and door trim before long, so why not buy it now and do our part to get the economy kickstarted.
The moving van business has evolved over the years. Nowdays, you rent the van (10-26 ft) for a one-way trip based strickly on miles and they give you a week-10 days depending on distance. U-Haul and Budget are common, but we prefer Penske. Their trucks are newer plus he's got a great racing team. The fuel costs are about as much as the move. For example, for this one we have a 16 ft van (two axle) that rents for about $900, and gas (8 mpg) will be about $650 (1500 miles = 185 gals at $3.50). With the 26 ft diesel we used for the main move, we spent about $900 on diesel (6.7 mpg commonly at $4.50+ two months ago) and $1200 for the truck. Because of the expert packing ability of Ren Thompson and Tony Crone (both USGS), not a single item was broken. The few scratches that occurred were the result of 1500 miles of bouncing around. There's nothing like 3 long days behind the wheel of a large truck to remind you what hemorrhoids are all about.
Update (10/23) We're back from our little trip to Colorado, which went well. Perfect weather, did some USGS business, and had a great time at the farewell party. Gas costs were a pleasant surprise, if you can say that. Gas was $2.62 at Rawlins, WY and high at Brigham City, UT ($3.25), but averaged about $3.00/ gal. Plus the truck got 10 mpg, so the return trip was about $450 for gas. The truck ran well, but Penske is in trouble with us for sending the truck out with two low tires (fronts, 20# each, one with a moderate leak), and a flat rear tire (duals). The flat was replaced quickly in Denver, but there office there was negligent in sending truck onto the road. More later as I vent with Penske Corporate.
The moving van business has evolved over the years. Nowdays, you rent the van (10-26 ft) for a one-way trip based strickly on miles and they give you a week-10 days depending on distance. U-Haul and Budget are common, but we prefer Penske. Their trucks are newer plus he's got a great racing team. The fuel costs are about as much as the move. For example, for this one we have a 16 ft van (two axle) that rents for about $900, and gas (8 mpg) will be about $650 (1500 miles = 185 gals at $3.50). With the 26 ft diesel we used for the main move, we spent about $900 on diesel (6.7 mpg commonly at $4.50+ two months ago) and $1200 for the truck. Because of the expert packing ability of Ren Thompson and Tony Crone (both USGS), not a single item was broken. The few scratches that occurred were the result of 1500 miles of bouncing around. There's nothing like 3 long days behind the wheel of a large truck to remind you what hemorrhoids are all about.
Update (10/23) We're back from our little trip to Colorado, which went well. Perfect weather, did some USGS business, and had a great time at the farewell party. Gas costs were a pleasant surprise, if you can say that. Gas was $2.62 at Rawlins, WY and high at Brigham City, UT ($3.25), but averaged about $3.00/ gal. Plus the truck got 10 mpg, so the return trip was about $450 for gas. The truck ran well, but Penske is in trouble with us for sending the truck out with two low tires (fronts, 20# each, one with a moderate leak), and a flat rear tire (duals). The flat was replaced quickly in Denver, but there office there was negligent in sending truck onto the road. More later as I vent with Penske Corporate.
Ruminations and subs
Well, now we know what it means to be the general contractor on a small (homeowner) job. You are generally the smallest fish in the pool and the subs are beholden to the large contractors and builders. We're having trouble with the concrete subs we've interviewed. The first one came in higher than we anticipated (based on virtually no data), so we were waiting for a second. That one was just a bit less and the sub didn't sound so interested (steadier jobs on the horizon, we think). A third sub hasn't called back after two contacts and the forth guy (local expert) wasn't even interested.
One problem is that this foundation work is complicated, largely the result of our structural engineer's (M. Brostrom) zeal for Simpson fasteners; he likes to make sure nothing is ever going to move, even in a Cascadia M8-9 earthquake. Thus, there are many structural fasteners (tie down bars, multiple courses of rebar), and keyways in the footers that are not usually seen. So this isn't going to be an easy-forms up & concrete-in job. Also, because there is a full depth basement (a Denver thing), we'll need 4-5 pours, three of which will require overhead pumping (separater rig that comes from 50 miles away). The bottom line is looking like 90 yds of concrete at $90/yr, a ton or two of rebar, 50-60 foundation to subfloor Simpson ties, and 4 weeks on the job. That's twice as long as we expected and puts the framing part of the job off until early December (cool, wet). So it goes.
Also, we need to know more about the actually concrete pouring process and schedule to get a reasonable bid on the excavation work, which precedes the concrete (obviously). For example, I imagine that the basement should be excavated first, then after the footer, 8' walls, perimeter drain and waterproofing is done, they would backfill and then excavate the crawl space (4 ft deep) and garage pad. The two excavation bids so far have all the excavation done at once and one backfill. Its not going to be this simple. More later.
[update 10/13/08]:
So today we settled on the foundation proposal. Don McNees of K&D concrete is going to do the work. We went with him for three reasons: 1) he recently did a job that was spec'd out by our structural engineer, so he's familiar with the details involved; 2) he was the most willing to discuss details, pitfalls, and the process of the four guys we contacted, and 3) he has worked a lot with our probable framers. So, after taxes we obligated $40k for concrete. However, when the big one (EQ) hits, our basement will be like the WWII bunkers at Fort Warden.
Now I need to settle on an excavator and make sure they can start on the hole around Oct. 27th, after the lot is cleared. Stay tuned.
One problem is that this foundation work is complicated, largely the result of our structural engineer's (M. Brostrom) zeal for Simpson fasteners; he likes to make sure nothing is ever going to move, even in a Cascadia M8-9 earthquake. Thus, there are many structural fasteners (tie down bars, multiple courses of rebar), and keyways in the footers that are not usually seen. So this isn't going to be an easy-forms up & concrete-in job. Also, because there is a full depth basement (a Denver thing), we'll need 4-5 pours, three of which will require overhead pumping (separater rig that comes from 50 miles away). The bottom line is looking like 90 yds of concrete at $90/yr, a ton or two of rebar, 50-60 foundation to subfloor Simpson ties, and 4 weeks on the job. That's twice as long as we expected and puts the framing part of the job off until early December (cool, wet). So it goes.
Also, we need to know more about the actually concrete pouring process and schedule to get a reasonable bid on the excavation work, which precedes the concrete (obviously). For example, I imagine that the basement should be excavated first, then after the footer, 8' walls, perimeter drain and waterproofing is done, they would backfill and then excavate the crawl space (4 ft deep) and garage pad. The two excavation bids so far have all the excavation done at once and one backfill. Its not going to be this simple. More later.
[update 10/13/08]:
So today we settled on the foundation proposal. Don McNees of K&D concrete is going to do the work. We went with him for three reasons: 1) he recently did a job that was spec'd out by our structural engineer, so he's familiar with the details involved; 2) he was the most willing to discuss details, pitfalls, and the process of the four guys we contacted, and 3) he has worked a lot with our probable framers. So, after taxes we obligated $40k for concrete. However, when the big one (EQ) hits, our basement will be like the WWII bunkers at Fort Warden.
Now I need to settle on an excavator and make sure they can start on the hole around Oct. 27th, after the lot is cleared. Stay tuned.
Friday, October 10, 2008
First subcontract
Well, we picked someone to fell the trees, clear the brush, and remove the stumps. In addition, the logs will be stacked perpendicular to the road for later pickup by a loader (this guy takes them to a mill and sells them for us minus his transport fees). The final bids ranged from about $8k to $13k, and we chose the $8k guy. He submitted the most detailed estimate and can start when we want, which for now is Oct. 24th. He'll move onto the site before that, then fire up the chain saw. I wouldn't normally take the low bid (of many), but this guy (Bill Snyder, Balco Trucking and Excavation) is a former logger that got into the landclearing and excavation business when the spotted owl issue got ugly on the west coast. So at heart, he's a tree feller--which is what we want. Also, he knows how to dissect the trees for the best resale (this is called scaling).
Wednesday, October 8, 2008
Trees and shrubs to go
This should be quite a challenge. There are some 110-15 ft high trees on the lot, up to 30" in diameter. Normally if you removed a single tree, a logger would climb the tree and take it down in 5-10 sections. However, with so many large trees they'd like to push them over on the lot, then cut them into marketable lengths (32' of 40') for resale. There are 3 large trees in the center of the lot, so for these they'll have to be cut in half, dropped and then recut. Sounds like a scarry proposition to me, but you have to assume that these guys know what there doing (not like our present crop of politicans).
The timber resale market is in the toilet now. Two foresters that visited the property estimate that the logs might fetch $1500-2000 at the mills (50-60 miles away), but loading and truck transport will eat up about half of that amount. So we'll be lucky to clear $1000 from the lumber after its all done and over with. 3 years ago, the market was twice as good as now. I learned a bit about lumber in this process. The best trees are straight doug firs in 50-60 lengths that are 16-10' in diameter: intended as power poles. These can go for upwards of $1500 each. We don't have any. Second best trees are peelers. These are large diameter trees with few branches, preferably in 20-32 ft long sections. They'll be debarked and turned, and then peeled as veneer for plywood. We don't have any. Third best trees are for standard 2x lumber, quality dependent on knots and other imperfections. We have lots of these. Call them mega-toothpicks. Probably $100 each for a big one. The least valuable trees are the smaller diameter and crooked ones. They'll be pulp wood for anything from OSB to cardboard or firewood. They're worth less than the cost to move, but they have to go somewhere and the landfill charges more. There you go—Lumber 101. Go into plastics, as they said.
The timber resale market is in the toilet now. Two foresters that visited the property estimate that the logs might fetch $1500-2000 at the mills (50-60 miles away), but loading and truck transport will eat up about half of that amount. So we'll be lucky to clear $1000 from the lumber after its all done and over with. 3 years ago, the market was twice as good as now. I learned a bit about lumber in this process. The best trees are straight doug firs in 50-60 lengths that are 16-10' in diameter: intended as power poles. These can go for upwards of $1500 each. We don't have any. Second best trees are peelers. These are large diameter trees with few branches, preferably in 20-32 ft long sections. They'll be debarked and turned, and then peeled as veneer for plywood. We don't have any. Third best trees are for standard 2x lumber, quality dependent on knots and other imperfections. We have lots of these. Call them mega-toothpicks. Probably $100 each for a big one. The least valuable trees are the smaller diameter and crooked ones. They'll be pulp wood for anything from OSB to cardboard or firewood. They're worth less than the cost to move, but they have to go somewhere and the landfill charges more. There you go—Lumber 101. Go into plastics, as they said.
Tuesday, October 7, 2008
First bids for land clearing
Well, we have 5 bids for clearing the land. This involved cutting the larger trees into marketable lengths (32-40'), felling all of them 60-70), stacking the logs (for loading and resale), brush cutting, leveling the land a bit, removing the debris, and building a short gravel-covered entrance and culvert. The bids are general to detailed, and range from about $7500-13,000. The cheapest one seems fine, but they always say to discount the cheapest and most expensive. One bid includes about $3000 for the foundation excavation and backfilling (which seems reasonable), so this may be the best bid. Need a bit more info to access the bids and make a comparison. We need to decide this week before returning to Denver for a week, so we can get the excavation and foundation guys lined up and on a schedule.
One neighbor is concerned that the falling trees will cause cracks in her foundation or walls. Seems unlikely, but we'll see. The largest trees are 115-120 ft firs and will have to be halved in order to drop them within the bounds of the property, which is 100-220 ft. Hopefully we'll have a skilled logger; hate to have a big one clip an adjacent house.
One neighbor is concerned that the falling trees will cause cracks in her foundation or walls. Seems unlikely, but we'll see. The largest trees are 115-120 ft firs and will have to be halved in order to drop them within the bounds of the property, which is 100-220 ft. Hopefully we'll have a skilled logger; hate to have a big one clip an adjacent house.
Monday, October 6, 2008
Approval process
Thursday, October 2, 2008
Our retirement home

In 2003, we decided to move to Port Townsend, WA when I retired (Aug. 2008). We bought a 0.6 acre lot ($40,000, 100' x 22') in the Kala Point subdivision, a gated community about 6 miles south of town. Its a lovely community in a heavily treed part of the Quimper Pennisula. The Pacific NW was new to us, with most of our friends in the Denver area and relatives in the SF Bay area. Our thought was that we'd have a potential pool of 450 families as friends and all the amenities that a HOA community gives. There is 1.5 miles of private beach, a boat launch and floating dock, as well as tennis courts, a swiming pool and clubhouse. The HOA fees are modest ($600/yr), which goes to maintain infrastructure in the subdivision.
By 2005 we had developed pretty firm ideas for our new house. We interviewed a few architects and picked Richard Berg of Port Townsend because he had a good reputation and knew many locals in the building trades. Berg Architects (http://richardbergarchitects.com/) started on building plans in the Spring of 2007, first with conceptual drawings and basic floorplans. He made some substantial changes to our plans, but keep the basic design elements and living spaces that we had envisioned. Darlene Keefe did all the CAD work, and prepared the 18 sheets for construction. We were planning a house of about 2000 square feet, but ended up with about 40% more from add ons.
In 2006, we hired Suzanne Martin of Miller Bay Water to prepare a septic design for the house. All houses in unincorporated Jefferson County are on septic and local wells, although we have water service from the Kala Point Water Co. She designed a pressure-system that has the drainfield in the front of lot and a reserve field in the rear. There are two tanks and about 200 ft of drain line--all designed for a 3-bedroom house if we ever decide to expand or convert some of the house (its being built as a 2 bedroom). In all, 8 septic percolation holes were excavated, in addition to four old ones from the previous owner (ca. 1992).
The plans we're completed in July 2008, and submitted to the Jefferson County (WA) building dept in early August. They had just a few changes and qualifications, but we basically flew thru the approval process in 6 weeks (plan approval was taking 3 months in the Spring of 2008 owing to staff reductions). So, we had a building permit on about Sept. 20th. Next step was to put our color and materials package together for the Kala Point Architectural Committee (aka the Color Commies). This is one of the potential downsides of a HOA. Nevertheless, there basic guidelines are designed to help protect everyone's home values from the errant double-wide or boat project. They require Earth Tone colors for the exterior materials, and minimal tree cutting to preserve the forest nature of the subdivision.
The house is going to be a NW Craftsman style, with a rock belt line on the street-view sides, stained cedar shingles above, and painted Hardieboard and singles on the back sides (not really viewed by anyone). The roof will be a dark colored 50-yr architectural asphalt composition shingle. There is about 2000 sq. ft on the main floor, an 800 sq. ft suite (visitors) upstairs, and an 800 sq. ft basement (not common here) for the utilities, wine cellar and storage). The garage is oversized at 730 sq. ft, but includes room around the margins for a shop and tool storage. My first post-construction project will be a 17' Pygmy Coho single kayak kit, which I bought, shipped to Denver and moved back to PT. Its got about 2500 miles on it now and never been in the water.
Subscribe to:
Posts (Atom)
Blog Archive
-
▼
2008
(27)
-
▼
October
(11)
- Pythagorean's theorem (Day 8 of 273)
- Oh boy, a big hole in the ground (Day 3 of 273)
- Ducks in a row (Day 2 of 273)
- Timber! Then boom and crash (Day 1 of 273 to build)
- A week off, final move from Denver
- Ruminations and subs
- First subcontract
- Trees and shrubs to go
- First bids for land clearing
- Approval process
- Our retirement home
-
▼
October
(11)
Subcontractors and Suppliers
- Balco Excav. (land clearing, Bill Snyder)
- Bill McCutchen's Mill (cedar trim)
- Blake Tile and Stone, Sequim (Judy Reno, Eldorado Stone, Tile)
- Bob Brown Plumbing (Bob & Josh Brown)
- Boise Cascade joists (from Carls)
- Carl's Building Supply (Mike, Melissa, Michele, Terry & Lawrence)
- Castlerock Landscaping (Tim Hamm, Sequim)
- Cotton RediMix (concrete and gravel)
- Craighead Electric (Gary Estes)
- Custom Hearth (propane fireplaces), Pousbo
- Daltile (Seattle, Wedi board)
- Discount Cabinets of Washington (Sequim)
- Discovery Bay Materials (gravel, top soil)
- Earl Kong (professional forester, PT))
- EcoHaus (Amer. Clay Plaster, cork flooring)
- Ellis Construction (Gary and Troy Ellis, framing)
- Evergreen Products (Drywall, Sequim)
- Fergusons, Seattle (Plumbing fixtures, Bud Allen Wright)
- FInlandia Saunas (Tigard, OR)
- Fitzgerald Concrete (driveway, Mike Fitzgerald)
- Four Corners Nursery (trees, Port Hadlock)
- Frank Feltes Custom Drywall and Painting (drywall and painting)
- Frank Ward and Wayne Jobst (Stone masons)
- Fredricks Appliances (Redmond, all appliances)
- Giraffe Gutters (Dan Shaw, Chimicum)
- Glass Etchings by Perrett (Jerry Perrett)
- Hadlock Building Supply (bits and pieces)
- Hardiboard, siding, backer board (from Carls and Home Depot)
- Henerys Hardware (Cabot stain, misc. fasteners)
- Hi-Tech Electronics (Audio & Media, Port Angeles)
- Hide-A-Hose (Joseph, A-B Vacuum, Puyallup, WA)
- Home Depot (electrical & plumbing supplies, interior paint)
- Home Storage Solutions (John Plake, PT)
- Hope Roofing (Pabco Paramont Advantage shingles)
- Jim's Tool Time (J. Quandt, misc. carpentry)
- K&D Concrete (Don McNeese)
- Kitchen and Bath Studio (Shelly Little, cabinets)
- Levi's Energy Services LLC (radiant design, vents, propane piping)
- Meta Marble and Granite (travertine), Seattle
- Michaelangelo (sepentinite), Seattle
- Mikael Brostrom (Structural Engineer)
- Mills Interiors (wood flooring, some tile)
- North Coast Electrical (Electrical Supplies)
- Olympic Garage Doors (Sequim)
- Penisula Flooring (carpet)
- Penisula Shower and Mirror (Sequim)
- PexSupply (online plumbing and radiant supplies)
- Puget Sound Power (and Atelco installers)
- Richard Berg Architects (Richard and Darlene)
- Richard Gifford Construction (septic, dry wells and grading)
- Richerts Marble and Granite (countertop fabricators)
- Seattle Lighting (lighting fixtures)
- Secret Gardens Nursery (Sheila Piccini)
- Shine Quarry (basalt for landscaping)
- Sierra Pacific Windows (Rob Sorg)
- Simpson Doors (from Carls)
- Simpson Strong Tie (fasteners & hold downs)
- Stewart Excavating (Mark Stewart, foundation)
- Sunshine Propane (propane and tank)
- Therma-Tru Doors (from Carls)
- Tracy's Insulation (batts and blow in)
- Trex Decking (from Carls)
- Trussworks (roof trusses, Carl's)
- Velux (Skylights and Solar tubes, Carls)
- Versalam beams (from Carls)
- Warmboard (Bruce Hull)
- Wisbo Aquipex, Taco Pumps, Polaris tank (Sunshine Propane)
Followers
About Me

- Kala Point Builder
- Professional geologist (USGS, 1972-2008), amateur home remodeler and now builder. Interested in sailing, all things involving salt water, woodworking, and food in general. Owner of Paleo Seis Surveys LLC, consulting in Quaternary geology and geological hazards.