Its Saturday, Halloween, and I'm hoping for treats not tricks. It rained buckets in Seattle yesterday, but not a drop fell on us in Port Townsend so I made some real progress in terms of painting the exterior of the hose. As you'll recall, all the shingles are up on the back of the house and now we need to get paint on them (upper level) and Hardiboard (lower level).
I fired up the "Ken Olsen Spray Tech 2120" rig, its a real monster. Feeds from a 5 gal bucket through a 50 ft hose. After reading the manual, I went to PT and got a replacement spray tip and a swivel extension, which saved my bacon. The extension is 3 ft long and allows you to spray a vertical pattern 10 ft high, so I didn't need to operate off a ladder on top of the scaffolding. I actually felt safe for a change. Anyway, after getting the rig set up and loaded with paint, I sprayed the entire north-facing section of the house (a triangle, 48 ft long and 12 ft high) in about 10 minutes! Then I back rolled it all (forces the paint into the shingles) with a 9" roller. I used a 6" foam roller to squeeze paint into the porous ends of the shingles so they'd be painted too. After about an hour, I reshot all the shingles with a light coat and back rolled it all a second time. Start to finish was about 4 hours, including a hour to clean up the sprayer. We're using oil-based stain (Cabots), so clean up is more complicated than latex.
Today, Darrell Olson (not a relative of Kens, but should be) is coming over so we can move all the scaffolding around to the back side of the house. Then I'll spray those shingles, break down the scaffolding, and start spraying the Hardiboard from ground level on Sunday. The weather forecast is for mild temps (50s) and decreasing rain through Wednesday, which is our current deadline for completing the exterior. Its looking like we'll be in for a treat ($1000 refund), not a trick (fines) from the Architectural Committee.
Nancy and I are starting our new careers as amateur landscape gardeners. A local nursery (Secret Gardens) is having their end of season sale through today, so yesterday we went down and picked out 7 trees and a dozen scrubs in exchange for a M-note. At 35% off, it'll save us some bucks, but plants are expensive if you want a yard that doesn't look Lilliputian. The idea is to get the bigger plants in the ground now so their roots will get established over the winter, then add foliage in the spring. The trees include a giant redwood, birch, 2 western red cedars, a colorful maple, and 2 flowering dogwoods. Now the trick will be to keep the deer from eating all the new growth in the spring. I'm thinking paint ball gun so we can scare and mark the vandals in one pull of the trigger.
Building a House in Kala Point, Port Townsend, WA
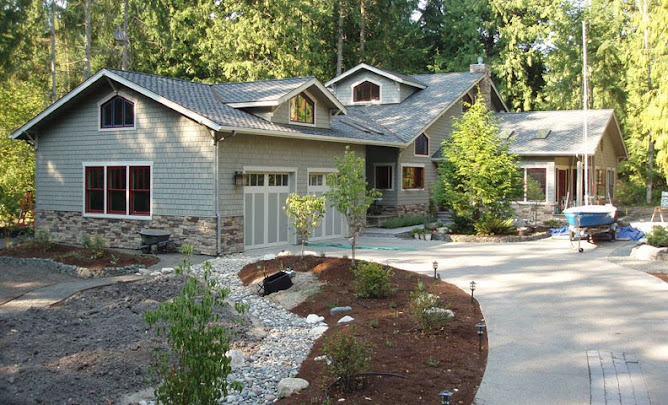
A running narrative of first-time builders of their retirement home in Port Townsend, WA (NE corner of the Olympic Pennisula, 60 miles NW of Seattle). Follow us as this adventure unfolds in late 2008 and beyond. 18 months under construction, we moved in on May 25th, 2010. Photo taken August 15, 2010.
Search This Blog
Saturday, October 31, 2009
Wednesday, October 28, 2009
Back in the Saddle (Day 367)
Well, not much has happened for two weeks. We took a break from building, partly for rest and partly because we had two trips planned. Did the GSA meeting in Portland for a long weekend, worked two days getting ready to paint the exterior, then headed off to Denver for a final trip.
The USGS wanted me to clean out my office on the off chance they might hire someone new, some day. One day of work and mission accomplished. Threw away the leftovers from a 35-year career, shipped 4 parcels to myself, one to Jeff Knott, and gave the other good stuff away. Then Ken Olsen had his 60th birthday so we couldn't miss that, followed by the Hobie Fleet Fall Party and a chance to see Steve and Judy. On Sunday we scooted off to South Dakota to see son Tom , Jenn, and the kids, then back in 24 hours. Returned home on Tuesday to find out that we'd had a couple inches of rain and more on the way. So, slow it goes for now. Next and final deadline is Nov. 5th for the exterior. If the sun shines, the airless sprayer is coming out and paint will be a flying onto the shingles and then the Hardiboard. Can't wait to finish this part of the project; then we can concentrate on the interior during the winter months. New move in date is May 1st, god, weather, and bank willing.
Nancy and I are agonizing over a basic paint color for the walls and ceilings. We'll narrow it down to 3 color choices tomorrow, then get 3 oz. samples from Home Depot and see which of the 3 we like the best. We need to coordinate the basic color with the American Clay plaster, the kitchen cabinets, red birch flooring and the fir trim (both of which will be natural). If we don't like the color, we can always repaint at a later date. Frank is scheduled to shot the whole house (but not garage) next week, so the paint has to be on site by Monday evening. It will take about 60 gals to do the whole house, then another 5 gallons for accent colors that we'll roller on at a later date.
Meanwhile, more pavers are on the way for the front walk, I'm looking at basalt boulders for some short walls that we need for landscaping, and we have to pick out a bunch of trees while the fall sales are on. No problem finding ways to spend money right now.
The USGS wanted me to clean out my office on the off chance they might hire someone new, some day. One day of work and mission accomplished. Threw away the leftovers from a 35-year career, shipped 4 parcels to myself, one to Jeff Knott, and gave the other good stuff away. Then Ken Olsen had his 60th birthday so we couldn't miss that, followed by the Hobie Fleet Fall Party and a chance to see Steve and Judy. On Sunday we scooted off to South Dakota to see son Tom , Jenn, and the kids, then back in 24 hours. Returned home on Tuesday to find out that we'd had a couple inches of rain and more on the way. So, slow it goes for now. Next and final deadline is Nov. 5th for the exterior. If the sun shines, the airless sprayer is coming out and paint will be a flying onto the shingles and then the Hardiboard. Can't wait to finish this part of the project; then we can concentrate on the interior during the winter months. New move in date is May 1st, god, weather, and bank willing.
Nancy and I are agonizing over a basic paint color for the walls and ceilings. We'll narrow it down to 3 color choices tomorrow, then get 3 oz. samples from Home Depot and see which of the 3 we like the best. We need to coordinate the basic color with the American Clay plaster, the kitchen cabinets, red birch flooring and the fir trim (both of which will be natural). If we don't like the color, we can always repaint at a later date. Frank is scheduled to shot the whole house (but not garage) next week, so the paint has to be on site by Monday evening. It will take about 60 gals to do the whole house, then another 5 gallons for accent colors that we'll roller on at a later date.
Meanwhile, more pavers are on the way for the front walk, I'm looking at basalt boulders for some short walls that we need for landscaping, and we have to pick out a bunch of trees while the fall sales are on. No problem finding ways to spend money right now.
Wednesday, October 14, 2009
Spray Away (Day 355)
Its Wednesday, Oct. 13. Approaching the one year date for the house, having felled the trees on our lot on Oct. 23, 2008. Doesn't seem that long, but then again there were some cold rainy days last winter that I'd prefer to forget.
This week I need to finish laying the shingles on the back of the house, but the hard part is finished now. I think there are about 3 bundles (75 sq. ft) left to hang. Then I need to spray all the shingles (above) and then the hardiboard (below). The paint goes on fast (like a gallon a minute), so most of you time is spent in preping the windows and vents, and moving scaffolding. If the weather holds, this should be done in a week or so.
The drywallers are done. Frank's no. 1 daughter put plastic over all the windows and installed doors in the house and will finish the garage this morning. Then daughter no. 2 will be by to clean up all the debris and mud boxes (about 20) before they shoot the PVA paint on the walls. PVA is a primer with vapor barrier in it. (Poly Vinyl Acetate is a professional primer sealer for new construction and all unpainted interior drywall and texture coatings. A proprietary formula that includes acetate instead of the usual acrylic which is an improvement for sealing out moisture and odors. Designed for the professional painter and for the quality conscious consumer. Formulated for excellent adhesion, even sealing and holdout, it provides a uniform foundation for alkyd or latex paint.) After this is dries, Frank will roll up his drywall texture machine (cement mixer with a pump on it) and start shooting the texture on all the walls that will get painted. Three walls will be left alone: 2 for American Clay plaster and one for the rock fireplace surround. So, if all goes well, the house will be back in our hands by Friday night. Off to Portland for the GSA meeting, where there is a special session to honor Michael's career in geology and a dinner to roast him. This is something that Jeff Knott cooked up—apparently its easy to impress (or fool) him since he's from LA. It'll be a welcome break from the house, an opportunity to see Portland and some old friends (including Bill and Mary Scott).
When we get back into the house on Tuesday, it'll be time to start spraying all the walls with another coat of primer (not PVA) and the finish coat of paint, which will be backrolled. That ought to be quite a workout for the old arms, but the house will start to look finished with color inside. If we paint all the drywall, that would be 16,000 sq. ft. I'm figuring 15,000 sq. ft at 250 sq ft/gal will require 60 gals of primer, 50 gals of the basic color paint, and 10 gals of highlight colors. At $15-20 a gallon (average), the paint bill will probably run $1800 to $2400. However, Home Depot offers contractor prices to everyone if you purchase $2500 or more. You need to set up an account, give them a materials list (paint, backer board, mortar, some tile, electrical outlets, etc), and they'll give you a bid at reduced rates (ca. 5-10% off). At those prices, paint and electrical suppliers can't complete. We'll see how it goes. Right now we're in a race between the checkbook, the end of the year (for taxes and income), and completing the house. I suspect the checkbook will lose.
This week I need to finish laying the shingles on the back of the house, but the hard part is finished now. I think there are about 3 bundles (75 sq. ft) left to hang. Then I need to spray all the shingles (above) and then the hardiboard (below). The paint goes on fast (like a gallon a minute), so most of you time is spent in preping the windows and vents, and moving scaffolding. If the weather holds, this should be done in a week or so.
The drywallers are done. Frank's no. 1 daughter put plastic over all the windows and installed doors in the house and will finish the garage this morning. Then daughter no. 2 will be by to clean up all the debris and mud boxes (about 20) before they shoot the PVA paint on the walls. PVA is a primer with vapor barrier in it. (Poly Vinyl Acetate is a professional primer sealer for new construction and all unpainted interior drywall and texture coatings. A proprietary formula that includes acetate instead of the usual acrylic which is an improvement for sealing out moisture and odors. Designed for the professional painter and for the quality conscious consumer. Formulated for excellent adhesion, even sealing and holdout, it provides a uniform foundation for alkyd or latex paint.) After this is dries, Frank will roll up his drywall texture machine (cement mixer with a pump on it) and start shooting the texture on all the walls that will get painted. Three walls will be left alone: 2 for American Clay plaster and one for the rock fireplace surround. So, if all goes well, the house will be back in our hands by Friday night. Off to Portland for the GSA meeting, where there is a special session to honor Michael's career in geology and a dinner to roast him. This is something that Jeff Knott cooked up—apparently its easy to impress (or fool) him since he's from LA. It'll be a welcome break from the house, an opportunity to see Portland and some old friends (including Bill and Mary Scott).
When we get back into the house on Tuesday, it'll be time to start spraying all the walls with another coat of primer (not PVA) and the finish coat of paint, which will be backrolled. That ought to be quite a workout for the old arms, but the house will start to look finished with color inside. If we paint all the drywall, that would be 16,000 sq. ft. I'm figuring 15,000 sq. ft at 250 sq ft/gal will require 60 gals of primer, 50 gals of the basic color paint, and 10 gals of highlight colors. At $15-20 a gallon (average), the paint bill will probably run $1800 to $2400. However, Home Depot offers contractor prices to everyone if you purchase $2500 or more. You need to set up an account, give them a materials list (paint, backer board, mortar, some tile, electrical outlets, etc), and they'll give you a bid at reduced rates (ca. 5-10% off). At those prices, paint and electrical suppliers can't complete. We'll see how it goes. Right now we're in a race between the checkbook, the end of the year (for taxes and income), and completing the house. I suspect the checkbook will lose.
Tuesday, October 6, 2009
Day of Reckoning (Day 347)
Well, Monday was the day of reckoning (9 month + 2 month extension) in terms of the Kala Point Architectural Committee, which meets today (Wednesday morning). I'm sure our house will be the topic of much discussion since we didn't exactly make our "finished on the outside" deadline. But from the attached photo, it looks done to me. (PS, don't look in back). The concrete driveway is curing and the forms come off tomorrow, so there won't be any visible signs of construction. If that doesn't satisfy the committee, then screw them. Nancy has been painting around the exterior doors and window in preparation for the BIG SPRAY JOB, which is a week or two away. I've been hanging more frickin shingles, and painting them around the edges so we can mask off the other stuff. I included Darlene's (Richard Berg Architects) 3-D sketch for comparison to what actually got built. Not bad if we say so.


Pouring the driveway was an education in itself. Call it Concrete 102, whereas the Foundation was Concrete 101. My professor was Mike Fitzgerald, a 60s'ish bearded biker with a big old soft spot for dogs (especially German Shepards) and Miller Genuine Draft beer. I came highly recommended but I had a hard time reaching him (was in divorce court then on a road trip--think Easy Rider). Anyway, he gave me a price, then we negotiated. I guess the guy liked us since we were doing a lot of the work ourselves, so we cut a deal involving some labor on my part & cash. Apparently, he's not inclined to make many more fiscal donations to the ex. After the deal was made, I called him and said I'd also like to pour a little pad for a shed in the back before the driveway went in. I formed it up and put the wire mesh and rebar in place. He came out, helped pour it and finished it off. I asked him what I owed him and he wouldn't say, but in the long run a case of Miller evened the score.
About the driveway concrete. Normally, you'd spec a standard concrete mix. That is 5 bags of cement per yard (cubic) and 3/4" aggregate (crushed is best). However, in Kala Point exposed aggregate driveways are popular and look really good. The downside is they are more expensive and sweeping them off is a pain, so most everyone has one of those hideously noisy leaf blowers. Looks like I'll be buying one, perhaps the electric (quieter) version. Our formula for the exposed aggregate went this way: 6 sacks of concrete, pea gravel (<3/8"), fiber, and heat. The fiber acts as a binder for strength and heat, in the form of sodium phosphate, quickens the initial cure so the concrete can be worked in cool weather. After the mud is poured (concrete talk), you spray the surface with sugar water to retard the curing of the surface. Coke, 7Up, molasses, etc. all work, but sugar water is cheap and easy to make. Depending on the mud mix and amount of heat added, it'll take 2-5 hours for the mud to set up enough to get on it. Then you take a stiff brush and hose and wash away the top layer of cement, thus exposing the aggregate. The result is a pebbly, dark concrete surface. Easier on the eyes and it has good traction.
Mike told me to negotiate the concrete price with our local supplier (to remain anonymous, for soon to be obvious reasons). So I made a visit to the local mix master, and you'd think I'd stepped into the 60's. A bunch of 60-70 year old guys in a plywood shack, chewing. I suspected that there was a poker game going on in an adjacent room. After a few warm up comments, I asked my familiar question: What sort of a deal can I get. Well, he said, for multiple loads I can get 5% off, and if I pay cash I can get another 8.4% off (that's exactly the same rate as the tax, what a coincidence). Well, I ordered 24 yards and went away smiling. When I went to pay yesterday, I handed over $2500 in cash, the mix master tore up the load tickets, and we called it even. No receipts, just like 24 yards (48 tons) of concrete evaporated.
So it pays to negotiate, ask a few questions, and be willing to supply the green stuff. If I'd used my first concrete guy, the bill would have been about $10.8k for labor and tax and another $2.8k for concrete, for a total of $13.6k. That's quite a driveway, I'd say. In the end, we spent $4.6k for labor, $20 for a case of Miller, and $2.5k for concrete, for a total of $7.12k. That makes up a bit for the $37k foundation last November at full price.
PS. We stayed away from Wednesday's committee meeting, but later on a neighbor came by and said that since we were so close to making the deadline that the committe had granted us another month extension. (Nov. 5). That was easy, but we're still not done with the shingles and painting. However, Nancy has dipped her final shingle (about 5,000), everything from here on will be sprayed thanks to Ken Olsen and his old airless sprayer (Happy Birthday, Ken). We've asked for a 6 month extension on the rental house (until May 1), and figure it will take most of that time to complete the interior (paint, trim, doors, hardwood floor, tile, showers, cabinets, and final electrical). The new schedule gives us some breathing room and time off to travel to California after Christmas and maybe a little side trip to warm water. Oh boy, we'll need it. Ciao for now.


Pouring the driveway was an education in itself. Call it Concrete 102, whereas the Foundation was Concrete 101. My professor was Mike Fitzgerald, a 60s'ish bearded biker with a big old soft spot for dogs (especially German Shepards) and Miller Genuine Draft beer. I came highly recommended but I had a hard time reaching him (was in divorce court then on a road trip--think Easy Rider). Anyway, he gave me a price, then we negotiated. I guess the guy liked us since we were doing a lot of the work ourselves, so we cut a deal involving some labor on my part & cash. Apparently, he's not inclined to make many more fiscal donations to the ex. After the deal was made, I called him and said I'd also like to pour a little pad for a shed in the back before the driveway went in. I formed it up and put the wire mesh and rebar in place. He came out, helped pour it and finished it off. I asked him what I owed him and he wouldn't say, but in the long run a case of Miller evened the score.
About the driveway concrete. Normally, you'd spec a standard concrete mix. That is 5 bags of cement per yard (cubic) and 3/4" aggregate (crushed is best). However, in Kala Point exposed aggregate driveways are popular and look really good. The downside is they are more expensive and sweeping them off is a pain, so most everyone has one of those hideously noisy leaf blowers. Looks like I'll be buying one, perhaps the electric (quieter) version. Our formula for the exposed aggregate went this way: 6 sacks of concrete, pea gravel (<3/8"), fiber, and heat. The fiber acts as a binder for strength and heat, in the form of sodium phosphate, quickens the initial cure so the concrete can be worked in cool weather. After the mud is poured (concrete talk), you spray the surface with sugar water to retard the curing of the surface. Coke, 7Up, molasses, etc. all work, but sugar water is cheap and easy to make. Depending on the mud mix and amount of heat added, it'll take 2-5 hours for the mud to set up enough to get on it. Then you take a stiff brush and hose and wash away the top layer of cement, thus exposing the aggregate. The result is a pebbly, dark concrete surface. Easier on the eyes and it has good traction.
Mike told me to negotiate the concrete price with our local supplier (to remain anonymous, for soon to be obvious reasons). So I made a visit to the local mix master, and you'd think I'd stepped into the 60's. A bunch of 60-70 year old guys in a plywood shack, chewing. I suspected that there was a poker game going on in an adjacent room. After a few warm up comments, I asked my familiar question: What sort of a deal can I get. Well, he said, for multiple loads I can get 5% off, and if I pay cash I can get another 8.4% off (that's exactly the same rate as the tax, what a coincidence). Well, I ordered 24 yards and went away smiling. When I went to pay yesterday, I handed over $2500 in cash, the mix master tore up the load tickets, and we called it even. No receipts, just like 24 yards (48 tons) of concrete evaporated.
So it pays to negotiate, ask a few questions, and be willing to supply the green stuff. If I'd used my first concrete guy, the bill would have been about $10.8k for labor and tax and another $2.8k for concrete, for a total of $13.6k. That's quite a driveway, I'd say. In the end, we spent $4.6k for labor, $20 for a case of Miller, and $2.5k for concrete, for a total of $7.12k. That makes up a bit for the $37k foundation last November at full price.
PS. We stayed away from Wednesday's committee meeting, but later on a neighbor came by and said that since we were so close to making the deadline that the committe had granted us another month extension. (Nov. 5). That was easy, but we're still not done with the shingles and painting. However, Nancy has dipped her final shingle (about 5,000), everything from here on will be sprayed thanks to Ken Olsen and his old airless sprayer (Happy Birthday, Ken). We've asked for a 6 month extension on the rental house (until May 1), and figure it will take most of that time to complete the interior (paint, trim, doors, hardwood floor, tile, showers, cabinets, and final electrical). The new schedule gives us some breathing room and time off to travel to California after Christmas and maybe a little side trip to warm water. Oh boy, we'll need it. Ciao for now.
Saturday, October 3, 2009
Tape and Mud (Day 343)
To be finished on the exterior, we have to paint all the raw shingles and Hardiboard (a week) with Ken Olsen's HD sprayer, hang 5 exterior light fixtures (1/2 day), finish the mudroom porch shingles and soffit boards and trim out the two skylights (2 days), and move all the construction stuff to the rear of the house, where it can't be seen. Looks like we'll finish all that about the time the drywall is complete, weather permitting. Its starting to get cooler and rainier—Fall is definitely here.
Inside the house its a mess. The drywall hangers have gone and the scrappers (2 young girls) got all the drywall scraps out of the house and off to the dump (5 pickup loads full; not so environmentally friendly, but gypsum is a natural earth product). Then they patched the paper covering all the floors (basement and garage too). The mudders arrived on Wednesday and started in with ernest. These two guys really fly through a house.

Subscribe to:
Posts (Atom)
Subcontractors and Suppliers
- Balco Excav. (land clearing, Bill Snyder)
- Bill McCutchen's Mill (cedar trim)
- Blake Tile and Stone, Sequim (Judy Reno, Eldorado Stone, Tile)
- Bob Brown Plumbing (Bob & Josh Brown)
- Boise Cascade joists (from Carls)
- Carl's Building Supply (Mike, Melissa, Michele, Terry & Lawrence)
- Castlerock Landscaping (Tim Hamm, Sequim)
- Cotton RediMix (concrete and gravel)
- Craighead Electric (Gary Estes)
- Custom Hearth (propane fireplaces), Pousbo
- Daltile (Seattle, Wedi board)
- Discount Cabinets of Washington (Sequim)
- Discovery Bay Materials (gravel, top soil)
- Earl Kong (professional forester, PT))
- EcoHaus (Amer. Clay Plaster, cork flooring)
- Ellis Construction (Gary and Troy Ellis, framing)
- Evergreen Products (Drywall, Sequim)
- Fergusons, Seattle (Plumbing fixtures, Bud Allen Wright)
- FInlandia Saunas (Tigard, OR)
- Fitzgerald Concrete (driveway, Mike Fitzgerald)
- Four Corners Nursery (trees, Port Hadlock)
- Frank Feltes Custom Drywall and Painting (drywall and painting)
- Frank Ward and Wayne Jobst (Stone masons)
- Fredricks Appliances (Redmond, all appliances)
- Giraffe Gutters (Dan Shaw, Chimicum)
- Glass Etchings by Perrett (Jerry Perrett)
- Hadlock Building Supply (bits and pieces)
- Hardiboard, siding, backer board (from Carls and Home Depot)
- Henerys Hardware (Cabot stain, misc. fasteners)
- Hi-Tech Electronics (Audio & Media, Port Angeles)
- Hide-A-Hose (Joseph, A-B Vacuum, Puyallup, WA)
- Home Depot (electrical & plumbing supplies, interior paint)
- Home Storage Solutions (John Plake, PT)
- Hope Roofing (Pabco Paramont Advantage shingles)
- Jim's Tool Time (J. Quandt, misc. carpentry)
- K&D Concrete (Don McNeese)
- Kitchen and Bath Studio (Shelly Little, cabinets)
- Levi's Energy Services LLC (radiant design, vents, propane piping)
- Meta Marble and Granite (travertine), Seattle
- Michaelangelo (sepentinite), Seattle
- Mikael Brostrom (Structural Engineer)
- Mills Interiors (wood flooring, some tile)
- North Coast Electrical (Electrical Supplies)
- Olympic Garage Doors (Sequim)
- Penisula Flooring (carpet)
- Penisula Shower and Mirror (Sequim)
- PexSupply (online plumbing and radiant supplies)
- Puget Sound Power (and Atelco installers)
- Richard Berg Architects (Richard and Darlene)
- Richard Gifford Construction (septic, dry wells and grading)
- Richerts Marble and Granite (countertop fabricators)
- Seattle Lighting (lighting fixtures)
- Secret Gardens Nursery (Sheila Piccini)
- Shine Quarry (basalt for landscaping)
- Sierra Pacific Windows (Rob Sorg)
- Simpson Doors (from Carls)
- Simpson Strong Tie (fasteners & hold downs)
- Stewart Excavating (Mark Stewart, foundation)
- Sunshine Propane (propane and tank)
- Therma-Tru Doors (from Carls)
- Tracy's Insulation (batts and blow in)
- Trex Decking (from Carls)
- Trussworks (roof trusses, Carl's)
- Velux (Skylights and Solar tubes, Carls)
- Versalam beams (from Carls)
- Warmboard (Bruce Hull)
- Wisbo Aquipex, Taco Pumps, Polaris tank (Sunshine Propane)
Followers
About Me

- Kala Point Builder
- Professional geologist (USGS, 1972-2008), amateur home remodeler and now builder. Interested in sailing, all things involving salt water, woodworking, and food in general. Owner of Paleo Seis Surveys LLC, consulting in Quaternary geology and geological hazards.