Building a House in Kala Point, Port Townsend, WA
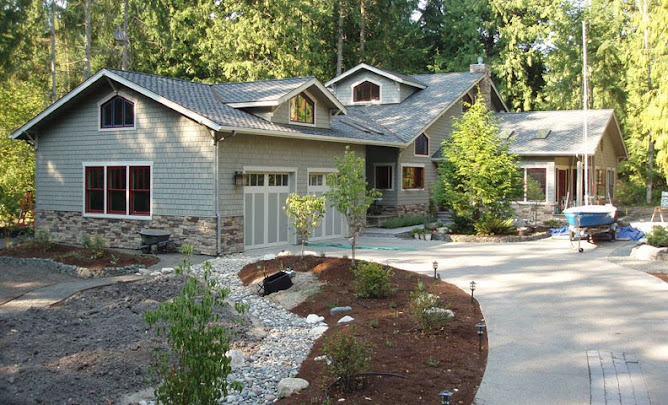
A running narrative of first-time builders of their retirement home in Port Townsend, WA (NE corner of the Olympic Pennisula, 60 miles NW of Seattle). Follow us as this adventure unfolds in late 2008 and beyond. 18 months under construction, we moved in on May 25th, 2010. Photo taken August 15, 2010.
Search This Blog
Saturday, January 31, 2009
4 & 8 barrel manifolds (Day 102 of 273)
Tuesday, January 27, 2009
Roof decking going on (Day 98 of 273)

All the major framing is done. In the photo to the left, Lonnie is securing the barge rafters (the ladder-like overhang on gable ends of the house) with another type of Simpson bracket. One every foot (with 8 screws), so no overkill here. Gotta watch out for those rogue NW Pacific hurricanes. Now the roof decking is going on. It is 5/8" OSB (actually its 19/32" to make life complicated), which we upgraded to the minimum code mandated 1/2" (7/16ths). Do you know of anything else that is labeled one sized and delivered smaller. 2x4s are 1.5x3.5. Its like buying a pint of your favorite lager and getting 13 oz. Anyway, we'll have a stiff roof to drive several thousand nails into. We're interviewing roofers this next week so that we can get it really watertight before the monsoon season hits (now until June).
The photos show the roof rafters (2x12s) on the bedroom/sunroom and decking on the 2nd floor and over the kitchen/sauna area. Notice the gable "love nest"; as previously mentioned naming rights are still available. The garage roof will be built next week; roof trusses should arrive on Friday morning. Beca of NW Trusses came over on Wednesday and measured all the critical things, then went back and fine-tuned the truss plan. She managed to make the room above the garage (lets call it the boat loft for fun) big enough to build an 18 ft kayak or canoe in, so I'm happy. The garage and mudroom roof gets built over the decking that already in place.
Last weekend I scouted out a local sawmill at the advice of Gary Ellis. Its a small shop owned by Bill McCutchen about 15 miles to the south out in the forest. He's been a fisherman in Alaska, then a contractor in PT, and now is running his own mill. He reminds me of a cross between Bryan Frahm (Hobie sailor and Kansas farmer) and Benjamin Bufford "Bubba" Blue (Forrest Gump's shrimper friend). Bill eats, drinks and breathes wood—any kind.

Monday, January 26, 2009
Garage walls up, rafters going on (Day 97 of 293)
Wednesday, January 21, 2009
Mikey's Thermoboards (Day 92 of 273)
1) Electric wall or baseboard heaters: Cheap to buy, expensive to operate and can be noisy (like at the rental house).
2) Hot water baseboard heaters: these can be attractive, a bit expensive, and require much hotter water (ca 160-180°F) than we'll be making in the basement (120°F for Warmboard). So that means buying a second water heater (boiler really), and that doesn't make any sense to us.
3) Radiant heating—Staple up. There are various companies that make systems for heating your space by stapling radiant tubing below the subfloor and insulating the joist cavity. The idea is that the heat moves up and through the floor: early versions were simply hot-water tubing attached to the subfloor. Now they prefer to use aluminum plates or sheets to spread the heat out, which works pretty well. The heat source (pipe) is still 1.5" away from your feet, but wood has an R value of 0.7-1.4/inch, so there isn't much resistance. These plates screw to the bottom of the subfloor and provide a track for the tubing. Typical products are include Joist Trak by Wirsbo ($2/sq. ft) and Thermofin C heat transfer panels ($3.50 sq. ft) by Radiant Engineering. The materials are commonly priced at about $6-10 a square foot, which is as much as the clearly superior Warmboard we used downstairs ($215 per 4'x8' sheet = $6.72 sq. ft). One problem with staple up is you need to snake 300 ft of semi-rigid Pex through holes in the floor joists, joist blocking, and any headers. You use 8" spacing, so 300 ft of pipe (max length per loop) only covers 200 sq. ft of floor. Plus all the work is overhead with ladders, which isn't pretty when middle-aged folks are involved.
4) Radiant heating—Above floor. In retrospect, we probably should have used the Warmboard upstairs too since the other (inferior) commercial products are nearly comparable in price. However, we went past that fork in the construction road several months ago and there's no point in looking back (sorry Bruce Hull, our Warmboard guy). Nevertheless, other above-floor options are out there. Two prominent ones are Quik Trak panels by Wirsbo and Raupanels by Rehau. The Quik Trak panels are 7" by 48 and screw down onto the subfloor. They price out at about $4/sq. ft (currently on sale). One problem with these is that they use 5/16" HePex O2-barrier tubing which is not compatible with co-mingled radiant and domestic water system. Same goes for the Raupanels, which are lower tech. The are basically 8" x 48" plywood panels with a groove routered down the middle for the Pex. The ends are pre-routered returns, so when its all laid out and screwed down it looks like a less eloquent version of Warmboard, but priced at about $11/sq. ft. The attractive part about above floor heating is how easy the tubing goes down. So I got thinking about a 4th option, which I like to call Mikey's Thermoboards.
4) Thermoboards (aka poorman's Warmboard). This is a hybrid version of Raupanels made out of 5/8" plywood. Technically, the piping gets laid out just like the Warmboard, but it doesn't have a continuous bonded-aluminum upper face. I'll rip 11 3/8" wide panels out of the 5/8" AC plywood (longways, 4 panels per sheet, ca. $35 each or about $1 sq ft.). The 1/2"AquaPex tubing (5/8" OD, $0.37/ft mail order) will go between the panels, for a finished width of 12" per panel. For the returns, I'll cut 12" x 48" panels from plywood, screw then down and use the router templates and bit that Warmboard supplied to make the return channels for each pipe run. I'll put a layer of aluminum under the panels (heat transmission) where I want it a bit warmer (bathroom) and cover the tubing with 10"-wide aluminum (comes in rolls, like the stuff they extrude gutters from now days). I can staple the aluminum down with my new airgun (Porter Cable from Tool King in Denver; it has a compressor, stapler, finish nailer and brad nailer; $229) and screw the panels in place with 1 1/8" drywall screws (ca. 800). Lots of labor, but like Pete Rowley (ex-USGS) was fond of saying "what is time to a pig." When you install the finished flooring, be careful to not nail through any of the aluminum or piping, and all is well (same goes with the Warmboard). The aluminum runs about $1 a square foot, so I think the finished Thermoboards (without tubing in them) will price out at $2.50 a sq. ft, which is 2/3rds to 1/4th the price of commercial options. Did I mention the No. 1 reason to build your own house: You can easily justify every tool you'd want to buy (new table saw comes next week, oh boy).
By the way, we've got a daytime security system in place. It has high-gain audio capability, search and retrieve options, and the ability to incapacitate intruders. It operates during working hours and is fueled by bacon, treats, and lunch scraps: a pretty efficient unit named Coal. He's Gary's buddy and worksite dog. He grew up on the job and, in fact, Gary has turned down framing jobs for people that aren't particularly fond of dogs.
Monday, January 19, 2009
Framing upstairs (Day 90 of 273)
On Friday they got the second floor exterior finished, and we're waiting for two large overhead beams to arrive on Monday. The big one is a 26-ft long 6 3/4" x 21" Gluelam and the shorter one (first floor bedroom) is a 22-ft long 5 1/4" x 18" Versalam. The gluelam is basically a sandwich of 2x6s, 14 of them glued together on their broad side. It weighs about 750 pounds, whereas the smaller Versalam only weighs 500 pounds.
So today is Day 90 of the build, which puts us at about 25% into our allowed 9 month (273 day) schedule. So far, so good. Once the roof is on (late February), the weather won't be a real factor and it should be getting warmer. Days are already noticeably longer (sunset at 4:30 pm) and by the vernal equinox on April 21, we'll have 12 hrs of sunlight ( fog permitting).
Monday, January 12, 2009
Making changes on the fly (Day 83 of 273)
Today the upper floor package should arrive from Carls. This includes about 30 floor joists, all the framing timber and some massive Versalam beams. The one that extends above the fireplace and supports the upstairs bedroom is 6"x16" and about 24 ft long. Looks like there might be a problem moving it around and lifting it into place. I put an order in for a sky crane and space hook. Stayed tuned.
THE BLIND CARPENTER
A blind carpenter walks into a lumber mill and shouts out, "I am a blind carpenter and I need a job."
The foreman walks over to the blind carpenter and says, "If you're blind, how can you work in a lumber yard?"
The blind carpenter says, "I can tell any piece of lumber by it's smell."
The foreman says "O.K. I'll give you a test and if you pass the test, you've got a job."
The foreman takes the carpenter over to a table and says, "I will put some lumber on a table in front of you and you tell me what it is."
The foreman then puts a piece of lumber on the table and says, "Ready!"
The carpenter bends over and takes a deep sniff moving his head from one side to the other. He says "That's a number two pine, two by four, eight foot long."
The foreman says, "Duh! That's right, but pine is easy to tell by the smell and I think you guessed the rest. Here's another piece of lumber for you to identify."
The foreman puts a piece of lumber on the table and says, "Ready!"
The blind carpenter bends over and takes a deep sniff moving his head from one side to the other and says, "This is a tough one, please turn it over so I can smell the other side."
The foreman does this and says "Ready!"
The carpenter takes another deep sniff moving his head from side to side. He then says, "That's a clear heart redwood, four by four, six foot long."
The foreman is amazed and says "That's right, but I still think you're just lucky and still guessing. If you get this one right you got a job."
The foreman then goes into the office and asks his secretary to help him stump the blind carpenter by taking off all of her clothes and laying down on the table. She takes off her clothes walks out of the office and lays face down on the table. The foreman says, "Ready!"
The blind carpenter takes a deep sniff moving his head from side to side. He looks puzzled and takes another sniff and says, "This also is a tough one, please turn it over so I can smell the other side."
The foreman gestures with his hand to the secretary, she rolls over, and the foreman says, "Ready!"
The blind carpenter moves his head from side to side again looking puzzled. He sniffs one more time, looks surprised, and says, "I got it. That's a shit house door off a tuna boat."
He got the job.
Thursday, January 8, 2009
The Blue Hole (Day 79 of 273)

When Nancy and I stayed at the Lake Quinault lodge last year, we were fasinated by their totum-pole rain gauge. It is a 20-ft-tall pole with a sliding gauge. In August they'd had 7 ft for the 2007 year, and in November they got 12 inches in one day. The rain comes into the lake so fast it can escape through the narrow natural spillway, to the lake can rise 8-10 ft overnight, inundating the campgrounds. All the houses and permanent structures are built at least 10 ft above the spillway elevation. Great place to visit, and the lodge is a USPS historic lodge.
Port Townsend gets about 17-18" of annual precip, as we do at Kala Point 5 airline miles south of town. We are in the south center of the Blue Hole. The Komo (Seattle TV Ch. 4) website (http://www.komonews.com/weather/faq/4306627.html) has a good discussion of the Blue Hole, but highlight the town of Sequim because it has the least rainfall (14") of all the towns. There is catcus growing on south facing slopes in Sequim, so they have a Denver-like climate without the snow and >80°F temps. However, you know what they say about Sequim. That's where the old folks go . . . to visit their parents. Enough said.

Wednesday, January 7, 2009
Dancing with the Subs (Day 78 of 273)
So today we'll try for a few more loops (4 of 9 to go). I bought a 20' x 30' tarp and a bunch of bungees and rope last night, hoping to tent over the next loop. That way we'll only have to clean and dry each section once. That the plan—let's see what Sub 3 has in mind. By the way, the forecast is for 10-20 inches (yes inches not cm) of rainfall in the Olympic Mtns for Wed and Thursday. They are about 50 miles SW of us, so we are praying for the famous Blue Hole to save us.
P.S. Thursday. I called Jason back to the jobsite to help me, since Nancy had to work today (I call it her day off when she works downtown). It rained in the am, so we constructed a tent over the floor and pressed on. Managed to get loops 6 & 7 done before lunch, then the wind came up and whipped the 20' x 30' tarp around like a bandana. However, that was followed by sun and dry weather, so we laid the last two loops (8 & 9) in record time. Finished about 4 pm, and spent the rest of my day cleaning up all the paper towels (5 rolls) and empty caulking tubes (52) that we scattered hither and yond. So, as of today (Jan. 8th), the house is back in the hands of Ellis Construction. Friday (tomorrow) is the framer's weekly construction meeting, which we've been invited too, at the Spruce Goose Cafe—7 am prompt. If we don't show up there will be a lot of owner/builder jokes told.
Sunday, January 4, 2009
Fast framers afoot (Day 75 of 273)
Once assembled, the three framers attach jacks to 12'-long 2x4s. The bottom of the 2x4s are nailed to blocking on the floor, and the jack is hooked to the top of the wall. The wall is wedged up a bit, and the jacking begins (Tony, these jacks are a variety of our famously dangerous Handyman jacks we used at the USGS). The sunroom wall went up first. Two jacks and about 5 minutes later it was in place. Next was the massive (58 ft. long) north wall. Three jacks and 10 minutes of jacking and it was up. Two shorter walls also went up, all in about 6 hours on Friday. The only glitch was a brain fart that Troy had. He'd left the plastic gas can next to the end of the long wall and when they jacked it up, the plywood skirt got caught on the can and compressed it. So they had to dig the gas can out, but put a hole in it in the process. No biggie, Home Depot has lots of them.
Monday they'll finish the exterior walls (but not garage, thats next) and tie them all together. Then its time for Nancy and I to do the Pex thing. We spent the weekend cleaning up the Warmboard. The channels were filled with frozen sawdust, nails and other construction flotsam, so this was quite a treat. The Pex is pretty rigid and isn't supposed to be installed below 40°F. The forecast is for warming weather, so we hope that around Tuesday and Wednesday well put all the radiant (Wisbo) tubing in place, but that's another blog.
Blog Archive
-
▼
2009
(91)
-
▼
January
(9)
- 4 & 8 barrel manifolds (Day 102 of 273)
- Roof decking going on (Day 98 of 273)
- Garage walls up, rafters going on (Day 97 of 293)
- Mikey's Thermoboards (Day 92 of 273)
- Framing upstairs (Day 90 of 273)
- Making changes on the fly (Day 83 of 273)
- The Blue Hole (Day 79 of 273)
- Dancing with the Subs (Day 78 of 273)
- Fast framers afoot (Day 75 of 273)
-
▼
January
(9)
Subcontractors and Suppliers
- Balco Excav. (land clearing, Bill Snyder)
- Bill McCutchen's Mill (cedar trim)
- Blake Tile and Stone, Sequim (Judy Reno, Eldorado Stone, Tile)
- Bob Brown Plumbing (Bob & Josh Brown)
- Boise Cascade joists (from Carls)
- Carl's Building Supply (Mike, Melissa, Michele, Terry & Lawrence)
- Castlerock Landscaping (Tim Hamm, Sequim)
- Cotton RediMix (concrete and gravel)
- Craighead Electric (Gary Estes)
- Custom Hearth (propane fireplaces), Pousbo
- Daltile (Seattle, Wedi board)
- Discount Cabinets of Washington (Sequim)
- Discovery Bay Materials (gravel, top soil)
- Earl Kong (professional forester, PT))
- EcoHaus (Amer. Clay Plaster, cork flooring)
- Ellis Construction (Gary and Troy Ellis, framing)
- Evergreen Products (Drywall, Sequim)
- Fergusons, Seattle (Plumbing fixtures, Bud Allen Wright)
- FInlandia Saunas (Tigard, OR)
- Fitzgerald Concrete (driveway, Mike Fitzgerald)
- Four Corners Nursery (trees, Port Hadlock)
- Frank Feltes Custom Drywall and Painting (drywall and painting)
- Frank Ward and Wayne Jobst (Stone masons)
- Fredricks Appliances (Redmond, all appliances)
- Giraffe Gutters (Dan Shaw, Chimicum)
- Glass Etchings by Perrett (Jerry Perrett)
- Hadlock Building Supply (bits and pieces)
- Hardiboard, siding, backer board (from Carls and Home Depot)
- Henerys Hardware (Cabot stain, misc. fasteners)
- Hi-Tech Electronics (Audio & Media, Port Angeles)
- Hide-A-Hose (Joseph, A-B Vacuum, Puyallup, WA)
- Home Depot (electrical & plumbing supplies, interior paint)
- Home Storage Solutions (John Plake, PT)
- Hope Roofing (Pabco Paramont Advantage shingles)
- Jim's Tool Time (J. Quandt, misc. carpentry)
- K&D Concrete (Don McNeese)
- Kitchen and Bath Studio (Shelly Little, cabinets)
- Levi's Energy Services LLC (radiant design, vents, propane piping)
- Meta Marble and Granite (travertine), Seattle
- Michaelangelo (sepentinite), Seattle
- Mikael Brostrom (Structural Engineer)
- Mills Interiors (wood flooring, some tile)
- North Coast Electrical (Electrical Supplies)
- Olympic Garage Doors (Sequim)
- Penisula Flooring (carpet)
- Penisula Shower and Mirror (Sequim)
- PexSupply (online plumbing and radiant supplies)
- Puget Sound Power (and Atelco installers)
- Richard Berg Architects (Richard and Darlene)
- Richard Gifford Construction (septic, dry wells and grading)
- Richerts Marble and Granite (countertop fabricators)
- Seattle Lighting (lighting fixtures)
- Secret Gardens Nursery (Sheila Piccini)
- Shine Quarry (basalt for landscaping)
- Sierra Pacific Windows (Rob Sorg)
- Simpson Doors (from Carls)
- Simpson Strong Tie (fasteners & hold downs)
- Stewart Excavating (Mark Stewart, foundation)
- Sunshine Propane (propane and tank)
- Therma-Tru Doors (from Carls)
- Tracy's Insulation (batts and blow in)
- Trex Decking (from Carls)
- Trussworks (roof trusses, Carl's)
- Velux (Skylights and Solar tubes, Carls)
- Versalam beams (from Carls)
- Warmboard (Bruce Hull)
- Wisbo Aquipex, Taco Pumps, Polaris tank (Sunshine Propane)
Followers
About Me

- Kala Point Builder
- Professional geologist (USGS, 1972-2008), amateur home remodeler and now builder. Interested in sailing, all things involving salt water, woodworking, and food in general. Owner of Paleo Seis Surveys LLC, consulting in Quaternary geology and geological hazards.